There is a clear need for refinery and offshore operators to reduce the complexity of large datasets into easy to visualise trends and correlations – Intertek InProcess provides a solution to this challenge.
The process industry collects large historical datasets. This data is complex and there are many interactions between variables which are not easily interpreted. This data has the potential to yield valuable information that can be used to improve performance. However, the quantity and noise from unrepresentative operations, such as process upsets and malfunctioning instrumentation, means that a challenge exists to unlock this.
Oil refineries have a clear need to reduce the complexity of large production datasets into trends and correlations that are easy to access and analyse. Tens of thousands of data points can often be at their disposal, presenting the challenge of how these can be viewed and analysed to yield meaningful information.
Our InProcess software application aims to simplify this process. It can import large datasets, offering the user an interface consisting of plots and summary tables. Features such as missing data, constant values, faulty sensors and questionable values can also be accessed through the system.
Intertek InProcess Software
Our proprietary technology software is designed to assist our clients in cleansing, ordering historical data and accessing valuable information that may positively impact processes and profit. When analysing data and making decisions based on variables, operations usually focus on first-order effects. For example, on platforms, flow rate into a vessel is known to have a direct effect on the level of the vessel, whereas the pressure sensors on a compressor would not typically be considered to. However, pressure drop across a compressor is indicative of compressor efficiency, which, in turn, has an effect on separator levels. In refineries, the flow rate of medium gas oil (MGO) is a function of many parameters such as reflux ratios, reboiler heat load and temperature of the feed - all first-order effects.
However, there are other factors affecting this which would not be directly linked to MGO production, such as the temperature of the desalter or the temperature of a slops stream being added to the crude blend. These both have an effect on CDU feed temperature.
There is a clear need for refinery and offshore operators to reduce the complexity of large datasets into easy to visualise trends and correlations – Intertek InProcess provides a solution to this challenge.
Data Purification
Intertek InProcess can import large datasets from data historians. It then gives the user an interface, consisting of plots and summary tables, to view this data. To maximise value from this, it is key to understand outliers and ‘clean’ datasets before additional analysis such as process modelling and optimisation. InProcess allows the user to examine the data and visualise any that may be missing, constant values, faulty sensors and questionable values. InProcess plots can be used to identify process outliers by looking at combinations of process variables.
Operating Regions
Intertek InProcess allows the user to visualise operating regions drawn from snapshots of the combinations of operating variables at a particular time horizon. Following identification, they can be correlated to key process variables. Operating regions can highlight process nuances such as decreasing process unit efficiency, shift changes and changing crude blend composition.
Key Process Variables
Intertek InProcess takes large datasets and displays the underlying trends in the process data and shows the variables which have maximum effect. It can pick out relationships caused by combinations of variables and other underlying effects, as well as the most obvious (first-order) relationships. However, process data is complex and there are many interactions. Statistical analysis uncovers the underlying combinatorial effects by selecting a target/objective function based on process requirements. For example, maximising flow-rate, minimising oily water overboard (for offshore) or maximising the production of diesel (at the refinery).
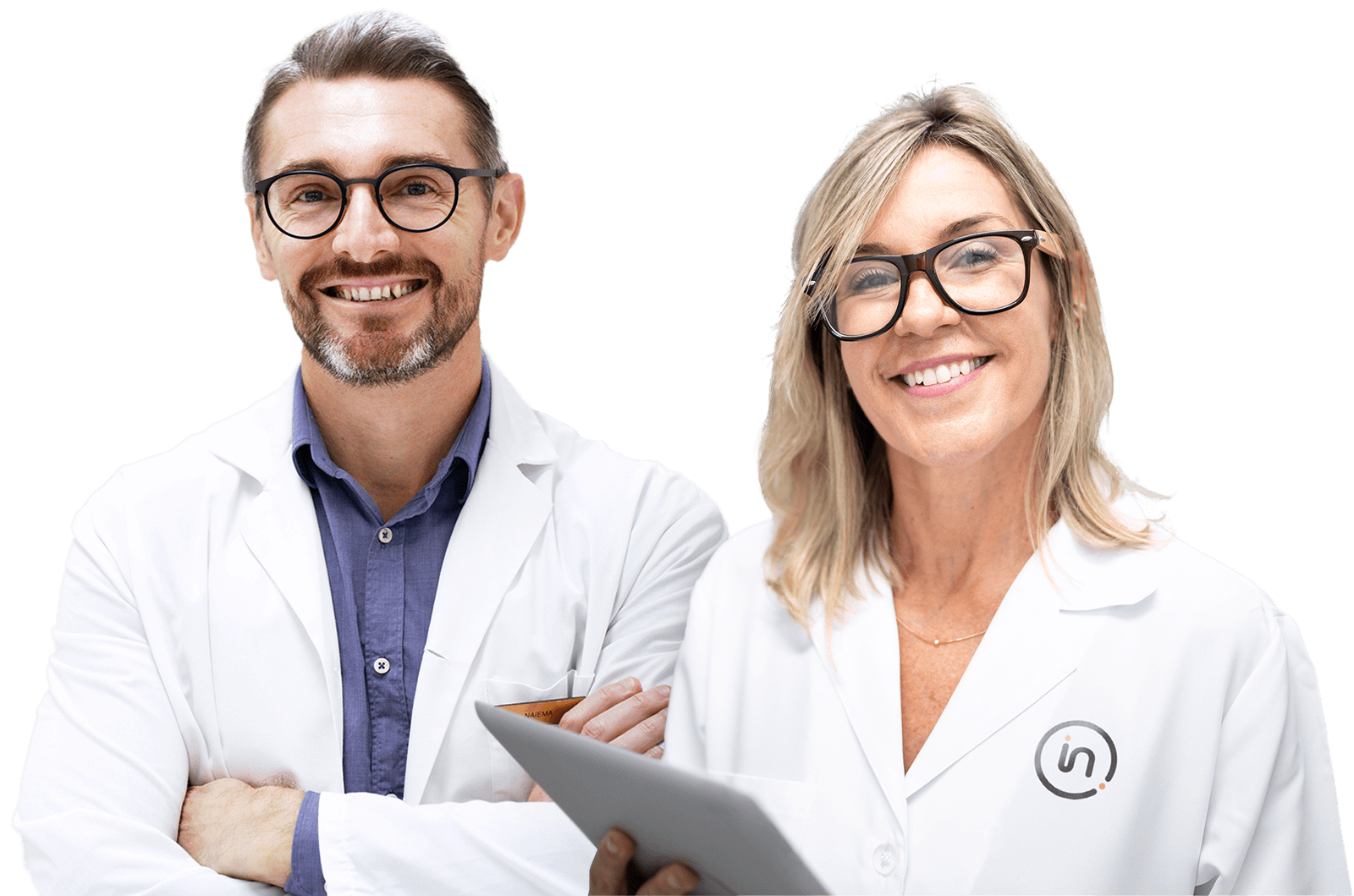