Vibration Testing: Fixtures
14 Jul 2020
Get It Right the First Time
Vibration testing is used across multiple industries as part of product development and testing to industry standards. In our previous blog post, we explored the fundamentals of vibration testing. When it comes to testing, many companies may choose to build their own fixtures, which could lead to unintended issues that can impact outcomes and increase costs. In this post, we explore some best practices to help get the fixturing right the first time.
First, it is important to consider some key concepts that apply to the entire testing system. This includes not only the product sample but the testing fixture and anything that may experience vibrations during the test. To ensure reliable results, one should consider the following:
- Transmissibility: The ratio of output to input. Force is transferred evenly regardless of how or where it is applied. In vibration testing, the amount of force and the material of the product are important. Does the product absorb the force? Dampen it? Will there be a rebounding effect when the force stops? Do you get out what you put in? More importantly, will the testing fixture withstand force? At what rate?
- Resonance: The output of a product's ability to accept or give off vibrations. When a product or testing system is in a free natural state, vibrations occur at its natural frequency. When force is applied to the product or testing system at this natural frequency, energy increases and releases, thus resonance occurs. To control this in a laboratory setting, a testing system (product sample and fixture) should be rigid enough that it can easily allow for the transfer energy without compounding that energy causing undue failures.
- Fixture stiffness: To ensure the system withstands force and provides a good level of transmission and resonance, and thus reliable results, it is important to ensure stiffness or rigidity. The natural frequency of the systems depends upon the stiffness and mass present.
Once these considerations are in place, move on to fixture design. Running a finite element analysis, or FEA, on the fixture will provide insight as to whether the system will break, wear out, or work the way it was designed while undergoing the vibration test. An FEA uses computers to predict and simulate how a product or system will react to real-world forces, like vibration. It will illustrate weak spots, stiffness, relationship issues and other concerns. The analysis can save time and money when conducting tests. Other things to keep in mind: material type, weight and thickness for stanchions, gussets and base plates; bolt placement, patterns and quantity; durability, mass and stiffness of attachments to the product sample and center of gravity and mass of the entire systems.
Expectations for fixtures are based on IEC 60068-2-64 and ISO 16750-3. They include:
- The natural resonance frequency of the loaded test fixture shall be above the upper frequency of the test profile
- The true value of the mechanical shock input as measured at the checkpoint for each sample, shall be within 10% of the intended value in the drive axis.
- The true value of the vibration, as measured in each intended axis at the checkpoint for each sample, shall be within 20% of the random vibration requirement.
Vibration testing can provide a wealth of information for products of all sizes in multiple industries. A thorough understanding of the process, including how to set up and run tests is critical to ensure success.
For more on considerations for fixturing for vibration testing, download our webinar recording.
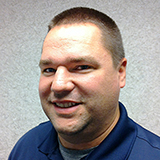
Mike Wells,
Sales Engineer
Mike Wells is a Sales Engineer with the Transportation Technologies division at Intertek. He has more than 15 years of experience in design and product validation testing. Mike is also an expert in the areas of Vibration, Mechanical Shock, and Electrical/Environmental testing. He is based at the Intertek facility located in Plymouth, Michigan.