Why Did My Part Break?
03 Mar 2020
A Look at the Failure Analysis and Investigation Process
If a product, component or asset fails or does not perform as expected, it can create quite a headache for manufacturers. Failures can result delays in product launches, added costs, regulatory issues, recalls, damage to the brand and company reputation, or even legal action. When a product or component fails, it is critical to understand how it happened—both the root causes and the events that led to the failure. Failure analysis testing provides the needed answers.
A failure analysis combines inspection, mechanical, physical, and chemical investigation to help determine the root cause of a failure. Failure analysis provides the insight needed to solve the problem, take remedial action and prevent recurrence. Using scientific approaches, the analysis gathers actional information to identify the physical root cause of a failure, such as material, manufacturing, or human reasons. It also provides insights needed for continuous improvement efforts and warranty analysis.
Failures commonly occur because of design flaws, material defects, service-life anomalies, manufacturing defects, and installation issues. Failure analysis can be useful to assess many of these issues and problems. For example, the most common type of failure in industrial, commercial, or consumer products is fracture and cracking. Failure analysis will determine the cause of these fractures, so it can be remedied with a new material, additive or design change. Cosmetic and/or functionality failures may also include discoloration, contamination, or corrosion. Chemical analysis can determine why such issues are occurring and how they can be prevented. Other failures include wear (on bearings, gears, etc.), distortion or deformation (such as warped metal or plastic component), adhesive, paint, and coating failures and product malfunction. A detailed and specific analysis can help address any of these issues.
Failure analysis typically involves some or all of the following steps: information gathering, visual inspection (with or without magnifications), non-destructive testing (function check, X-Ray, EDS analysis, etc.), destructive testing (chemical, mechanical, dissection for in-depth examination), a combination of customized analytical techniques, data review and conclusion/discussion. These components are combined to create a detailed report on the failure and to propose suggestions for solving the problems and fixing the errors.
Providing as much background information as possible to the failure analysis team is important to any investigation. This might include blueprints, manuals, material specifications, service environment, temperature, pressures, working conditions, failure symptoms, at what stage the failure occurred, , history of failure, previous testing data, inspection details and maintenance records. Such background information is used to guide test selection and, ultimately, determine the cause of failure. It's also critical to protect the failed part and provide good reference samples for a comparative study. If there are multiple failures, examining additional failed samples will allow identification of similar or different failure modes.
Often, a failure analysis can pinpoint the exact cause of the failure, identifying why the material, component or product failed. It can improve engineering and management decisions, product design and product life. In turn, this can mean a more successful product and strong brand reputation. Learn more about failure analysis and get answers to frequently asked questions about the process in our complimentary fact sheet.
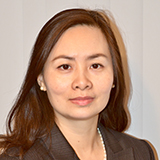
Helen Xiang,
Failure Analysis Department Manager
Helen Xiang is a department manager at Intertek, where she has worked for 15 years. Previously, she serves as the chief metallurgist and failure analyst, leading a multi-discipline team in subject ranging from raw materials, metals or plastics, to end user products. Besides standard metal or plastic product failure analysis, the team's specialties include emission, batteries and electrical product failure investigation. Helen holds a Ph.D in Materials Science and Engineering and a Masters in Mathematics, both from the University of Kentucky.