Intertek Blog
The Intertek Blog is a trusted source for insights on product safety, quality, sustainability, innovation, and compliance. The articles written by our experts explore industry trends, emerging technologies, regulatory developments, and best practices, delivering the knowledge and perspective you need to stay informed and inspired.
Most Recent Posts
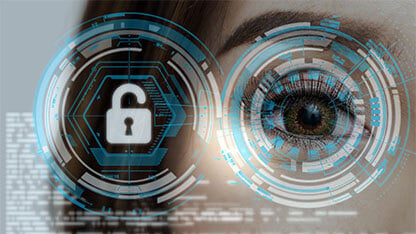
15 Jul 2025
RED Directive: The Cybersecurity Compliance Countdown – Part 9
Lessons Learned & What’s Next
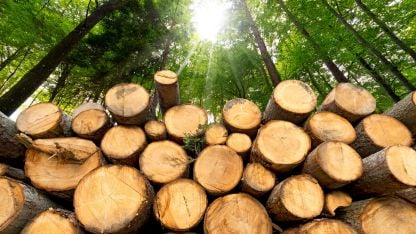
14 Jul 2025
What’s New in EUDR Guidance: Understanding Complex Requirements
Discover the Latest Guidance and Learn How it Streamlines the Compliance Process
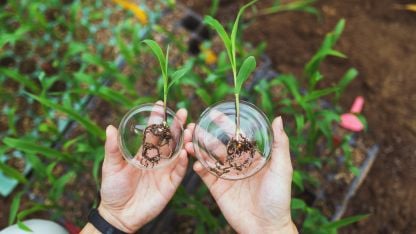
11 Jul 2025
Preparing for Reasonable Assurance of Climate-Related Disclosures (Part 2)
The Journey to Climate Assurance Readiness
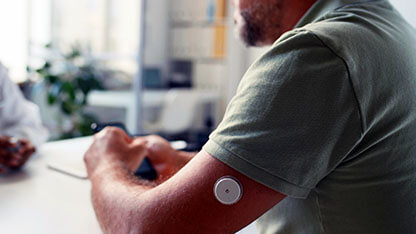
10 Jul 2025
Why Performance Testing is Critical for Modern Medical Devices
As devices become smaller, smarter, and more mobile, performance testing ensures they deliver when and where it matters most
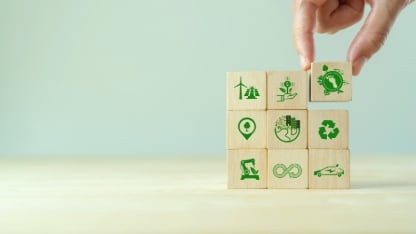
09 Jul 2025
Unveiling the Future of Textile Sustainability: Key Insights into the New PEFCR (Focus on Annex V & Product Scope)
Explore the EU’s new PEFCR for Apparel and Footwear, detailing Annex V durability standards, circularity focus, microplastic impact assessment, and comprehensive product scope. This science-based framework enhances transparency and supports compliance with upcoming EU sustainability regulations.
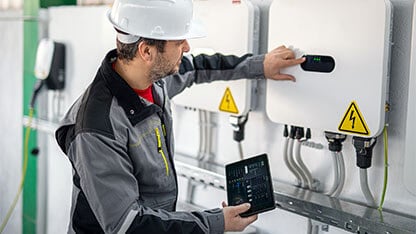
08 Jul 2025
Uncovering Hidden Risks in Renewable Energy Equipment
How to detect, prevent, and respond to cybersecurity threats
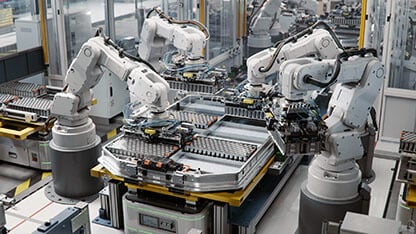
03 Jul 2025
Essential Safety Requirements: What You Need to Know About the New EU Machinery Regulation
Bringing Safety into the Digital Age
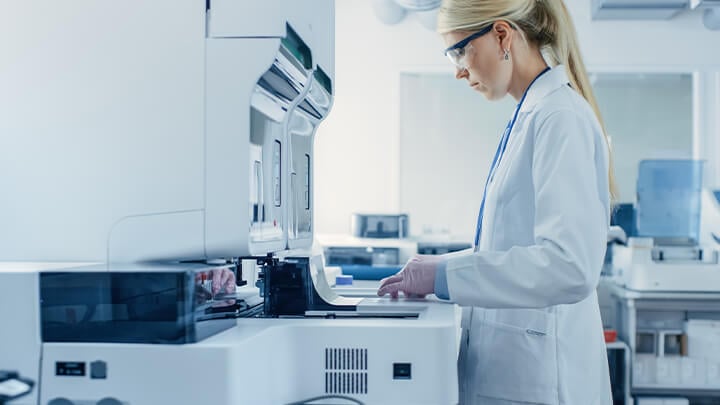
02 Jul 2025
What are the benefits of C-14 testing for different international markets?
To meet the growing demand for services, particularly in sustainable fuel sectors, our Caleb Brett fuels and aviation lab now provides advanced Carbon-14 (C-14) analysis testing aligned with ASTM D6866 standards.
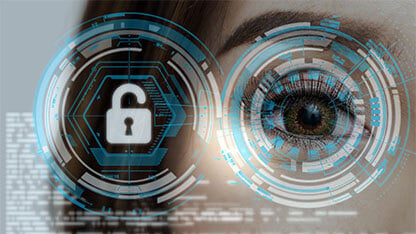
01 Jul 2025
RED Directive: The Cybersecurity Compliance Countdown – Part 8
Final Countdown: A 30-Day Compliance Checklist
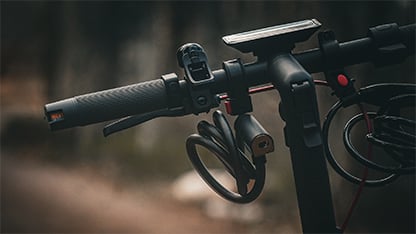
27 Jun 2025
Navigating 2027 requirements for removability and replaceability of batteries in electrical products
Increased focus on repairability for products using portable and LMT batteries
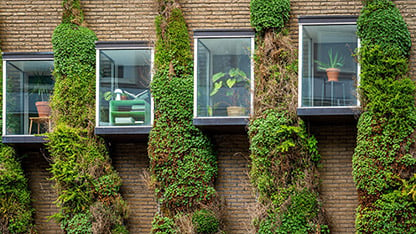
26 Jun 2025
Resilience Takes the Lead in LEED v5
The latest LEED update centers on climate risk, carbon reduction, occupant health, and equity
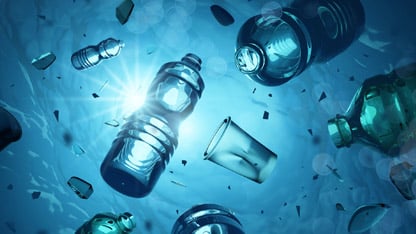
25 Jun 2025
Canada’s Federal Plastics Registry: Phase 1 Deadline Is Fast Approaching
A key initiative to monitor and track the lifecycle of plastics.
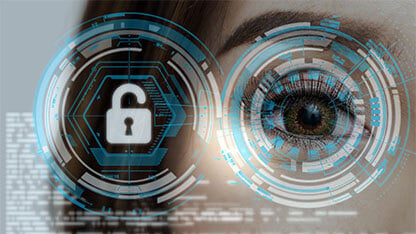
24 Jun 2025
RED Directive: The Cybersecurity Compliance Countdown – Part 7
Future-Proof your Products by Bridging RED and the Cyber Resilience Act
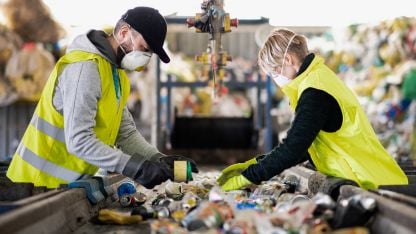
23 Jun 2025
Recycled Plastics in Electronic Products and Textiles: Sustainability, Compliance, and Safety
Learn how to use recycled plastics in electronics and textiles in a safe and compliant manner.
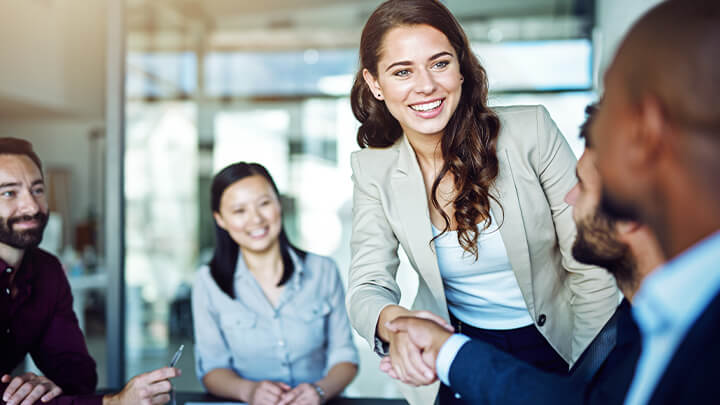
18 Jun 2025
Transferring Your ISO Certification Doesn’t Have to Be Difficult - Here’s Why
At Intertek, we believe that certification should empower your business, not burden it. In this blog we aim to dispel the myths, highlight how straightforward the process really is and explain why Intertek makes it easier than most.