Intertek Blog
The Intertek Blog is a trusted source for insights on product safety, quality, sustainability, innovation, and compliance. The articles written by our experts explore industry trends, emerging technologies, regulatory developments, and best practices, delivering the knowledge and perspective you need to stay informed and inspired.
Most Recent Posts
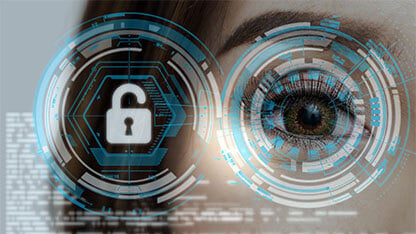
01 Jul 2025
RED Directive: The Cybersecurity Compliance Countdown – Part 8
Final Countdown: A 30-Day Compliance Checklist
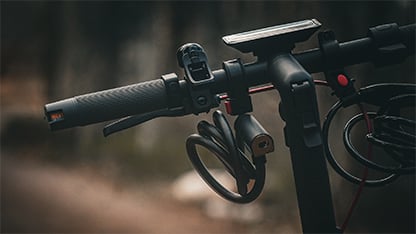
27 Jun 2025
Navigating 2027 requirements for removability and replaceability of batteries in electrical products
Increased focus on repairability for products using portable and LMT batteries
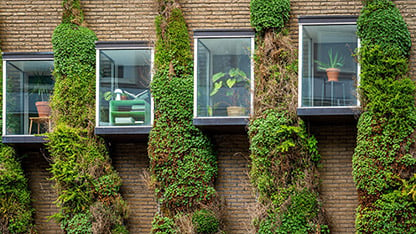
26 Jun 2025
Resilience Takes the Lead in LEED v5
The latest LEED update centers on climate risk, carbon reduction, occupant health, and equity
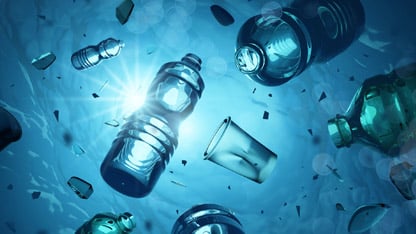
25 Jun 2025
Canada’s Federal Plastics Registry: Phase 1 Deadline Is Fast Approaching
A key initiative to monitor and track the lifecycle of plastics.
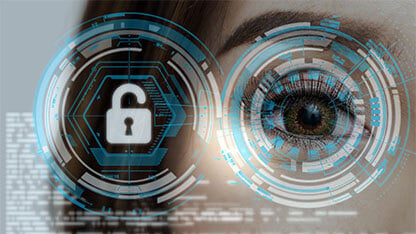
24 Jun 2025
RED Directive: The Cybersecurity Compliance Countdown – Part 7
Future-Proof your Products by Bridging RED and the Cyber Resilience Act
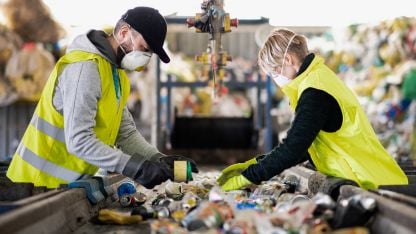
23 Jun 2025
Recycled Plastics in Electronic Products and Textiles: Sustainability, Compliance, and Safety
Learn how to use recycled plastics in electronics and textiles in a safe and compliant manner.
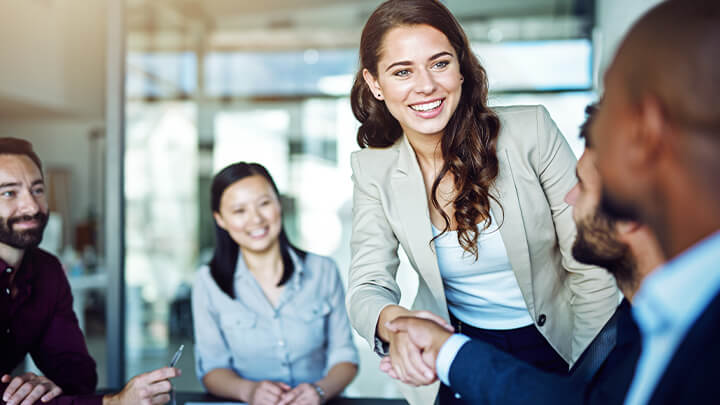
18 Jun 2025
Transferring Your ISO Certification Doesn’t Have to Be Difficult - Here’s Why
At Intertek, we believe that certification should empower your business, not burden it. In this blog we aim to dispel the myths, highlight how straightforward the process really is and explain why Intertek makes it easier than most.
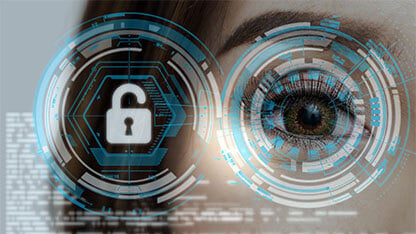
17 Jun 2025
RED Directive: The Cybersecurity Compliance Countdown – Part 6
Staying Compliant After Launch Using Post-Market Surveillance Mechanisms
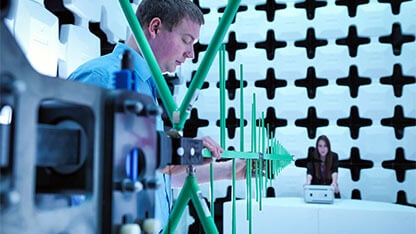
17 Jun 2025
Understanding the 2023 Updates to the CSA C22.2 No. 301 Standard – Part 3
Industry Canada Requirements for Electromagnetic Emissions
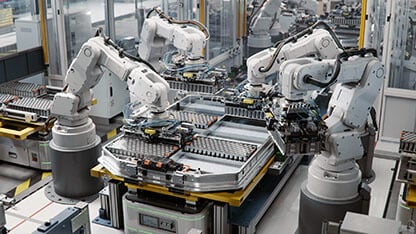
16 Jun 2025
What the Machinery Regulation Shift Means for Harmonized Standards and EHSR Compliance
Understanding the evolving landscape of EU standardization is essential for navigating this transition effectively
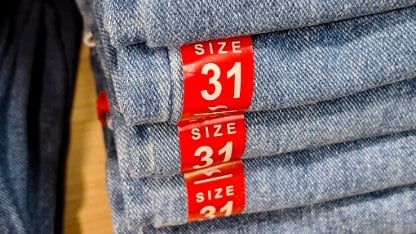
12 Jun 2025
Understanding BPS Exposure Risks in Apparel Tags and Stickers
With rising regulatory focus on BPS exposure from apparel tags and stickers, brands must review materials and switch to BPS-free thermal papers, inks, and adhesives to ensure compliance and consumer safety. Read the blog to learn more.
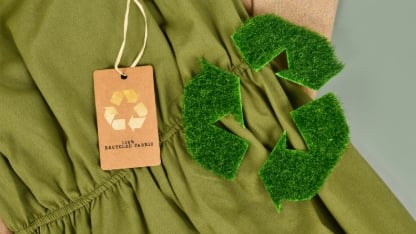
12 Jun 2025
The French Environmental Cost: Driving Transparency in the Textile Industry
The French Environmental Cost eco-score labels apparel’s environmental footprint based on 16 lifecycle indicators. Effective 2025, it promotes transparency and circularity.
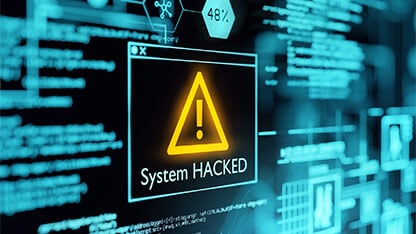
10 Jun 2025
Infostealers and Ransomware: Why Organisations Must Monitor the Dark Web as Ransomware Threats Rise
Being Proactive Equips Companies with the Intelligence to Act Early, Reduce Risk, and Protect their Data
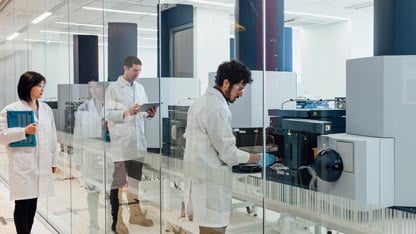
04 Jun 2025
Understanding Regulatory Frameworks for Single-Use Systems: USP <665>, USP <1665>, and BPOG Extractables Guidance in Biopharmaceutical Manufacturing
What pharma and biopharma manufacturers need to know – and do – before the 2026 deadline.
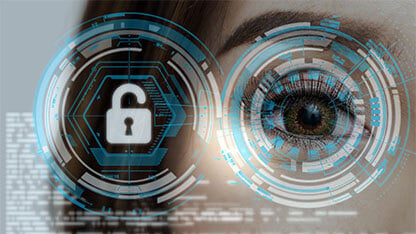
03 Jun 2025
RED Directive: The Cybersecurity Compliance Countdown – Part 5
Lessons from the Field on Closing Compliance Gaps