A Look to the Future of Formula E Racing
17 Feb 2022
How Formula E teams can extract maximum performance from their powertrains under the new regulations
The third generation Formula E electric vehicle racing is due to begin in 2023, and it features an all-new chassis design as well as an overhaul of the permitted maximum power levels. The power limit in races will increase from 200kW (Season 7, 2021) to 300kW whilst qualifying will see 350kW of available power, up from 250kW (Season 7, 2021). Front axle regenerative braking will also be introduced which means there is potential for combined energy recovery of up to 600kW (350 rear, 250 front). This additional element should further improve in race efficiency and extend the range of the battery.
As we embark on the next season of Formula E, each team will be looking for new opportunities to enhance their cars and maximise on-track performance. At Intertek, our automotive testing experts are passionate about motorsport and supporting Formula E teams to push the boundaries of what's possible in their vehicles.
Why does Formula E matter?
Formula E is about to embark on its eighth season. Having recently been recognised by the FIA, the governing body of motorsport, as an official world championship, it is growing ever stronger as a platform for promoting the capabilities and potential of electric vehicle technology.
Competition is an extremely effective driving force for technological advancement in motorsport. For years, technology developed in Formula 1 has found its way onto road cars, and now Formula E is joining the party. Several automotive manufacturers are competing in Formula E, and what they are learning is helping to shape the cars that consumers will be buying in the near future. Powertrains that can achieve efficiency values more than 98% are commonplace in current Formula E. When these are combined with higher power density batteries, electric vehicles can travel further whilst wasting less energy. Other improvements in inverter, motor and battery technology are helping to shape electric vehicles for the road.
What is needed for success in Formula E?
There is an adage in motorsport; "If you want to finish first, first you need to finish". It sums up perfectly the need for reliability above all else. With this in mind, it takes a strong, dedicated team to put together a car that is both quick and efficient. If we think of the battery as a bucket of energy, it is desirable to use as much of that bucket as possible to power the car forward, rather than making things hot and wasting energy as heat. That's where the need for an efficient and reliable powertrain comes in. When that's underpinned by a mechanically solid chassis, the result is a race car that combines high performance, efficiency, and reliability. In a nutshell, all three of these are required to achieve success in Formula E.
How can Intertek support Formula E teams?
At Intertek's brand-new EV test facility, we have a variety of rigs that can support a number of tests ranging from early powertrain development all the way through to reliability, efficiency tuning, and lap simulation. We also have a full car dyno capable of being operated as two separate E-axle rigs to facilitate testing of rear-end assemblies. All our rigs feature 400kW battery simulators, whilst the 4WD cell has 3 that can be run in various configurations to achieve power levels of up to 1.2MW.
As efficiency is a critical part of Formula E, it is vital to understand the characteristics of a powertrain in order to adopt the optimal race strategy. All the test rigs utilise HBM torque transducers, which when combined with our Yokogawa power analysers, can give very accurate and repeatable efficiency measurements. This makes efficiency mapping possible and is a good place to start in terms of understanding the powertrain. Average lap efficiencies can also be calculated by replaying real lap data on the test rigs to simulate on-track conditions. Powertrain characterisation can also play a big part in maximising efficiency, and the power analysers are capable of capturing raw data at 500kHz, which gives a detailed insight into how the powertrain is performing electrically.
Testing carried out on an E-axle rig can give teams a better understanding of how the drivetrain works as a whole. Overall efficiencies can be calculated, and this can lead to other avenues for maximising efficiency such as testing different gearbox architecture, lubricants, and drive shaft arrangements. Event simulation testing can also be carried out to make sure all of the components are capable of surviving as long as they need to. If the full 4WD rig is used, we can shakedown the whole car and test the ancillary systems including brake by wire and cooling.
Can Intertek support 3rd generation regulations?
Intertek's 4-wheel drive dyno is capable of running a whole car by driving as well as absorbing power so all aspects of the powertrain can be tested to the maximum power levels. When track testing time is limited, this testing can be a valuable resource in understanding and improving car performance. If the drivetrain is optimised off track, on track running can be focussed specifically on vehicle dynamics and operational gains.
For Formula E teams who are interested in testing their e-motor and inverter, by pushing the boundaries of the speed envelope Intertek can offer 1E test beds with a maximum speed of 27,000 rpm. These high-performance, low inertia PMSM driven test beds utilise pallet mounting systems that are completely independent in terms of power, cooling circuit, HVAC and SW control.
Intertek Transportation Technologies: We're Here to Help
Intertek's UK Transportation Technologies division has high quality testing facilities for EV and Hybrid powertrain, EV fluids, Transmission, and Fuel and lubricants, combining extensive industry expertise with world-class testing capabilities. With a diverse range of equipment across both its Milton Keynes sites, Intertek's specialist teams are helping manufacturers of motorsport and passenger vehicles to optimise their products.
To learn more about Formula E powertrain developments, read our white paper or click here to explore our extensive testing and consultancy capabilities.
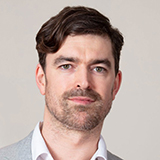
Ben Mitchell,
Senior EV Test Engineer
Ben is a Senior EV Test Engineer working in Intertek's new Global EV Centre of Excellence. Prior to joining Intertek, Ben worked in a range of automotive and aerospace engineering roles, including six years with Williams Racing working on both Formula E and Formula 1 testing.