Phased array is an advanced method of ultrasonic testing and can be used for a multitude of different inspection tasks.
Present day structural assessment, flaw analysis, fitness-for-service assessment and engineering critical assessments require flaw data in a more accurate and precise way with regard to their location, shape and size. Phased array ultrasonic technology with its associated flaw evaluation software can provide flaw data accurately and precisely for the fracture mechanics based acceptance standard.
This technique is used to detect flaws that cannot be easily found with conventional non-destructive testing methods such as radiography and manual ultrasonic testing. Intertek specialises in the use of phased array in the oil and gas, power generation and chemical industries, especially for the construction of new piping, pipelines, vessels and structural welded members providing Total Quality Assurance. We also use the technique in petrochemical plants, when quick and accurate inspections are necessary due to time constraints during outages.
A phased array probe is made up of multiple small ultrasonic transducers, each of which can be pulsed individually. By varying the timing of the pulse of each individual transducer, the ultrasonic beam can be ‘steered’ to a specific angle and focal distance – i.e. the beam can be swept through the examined object.
Applications for phased array:
- Weld inspection
- Volumetric inspection of forging or casting materials
- Erosion and corrosion mapping
- Scanning highly complex geometry components (for example, turbine blade roots and dovetails)
Flaws that phased array can detect:
- Weld flaws such as lack of fusion, slag inclusions, porosity, inside diameter / outside diameter (I.D./O.D.) cracks, centreline cracks and incomplete penetration
- Erosion or corrosion – pitting, material loss and root erosion
- Inherent discontinuities in forged or casting materials such as laminations, forging bursts, cold shuts, hot tears and inclusions
- Environmentally or process induced damage such as MIC, HIC, thermal fatigue cracking, caustic cracking and stress corrosion cracking
Phased array has several advantages in comparison to other non-destructive techniques. It allows for faster examinations compared to manual ultrasonic testing. Information can be displayed in multiple display formats (for example, A, B, C and D scans), which help in more accurate interpretation of flaws. The data can also be captured and stored so it can be reviewed by the inspector and used for future reference and inspections. A further benefit of phased array is safety. There is no radiation or environmental hazards compared to radiography. With phased array there is no need to shut down operations due to radiation exposure so there is less wasted man hours and increased production.
Intertek’s phased array inspectors are highly qualified, holding a minimum of ASNT (American Society of Non-destructive Testing) Level II or PCN (Personnel Certification in Non-Destructive Testing) Level 2. Additional industry certifications such as API QUPA and EPRI certifications are part of our continued training to ensure our inspectors are qualified to the highest industry standards. Our phased array inspectors undergo regular training to stay on top of the latest advances in phased array technology and techniques.
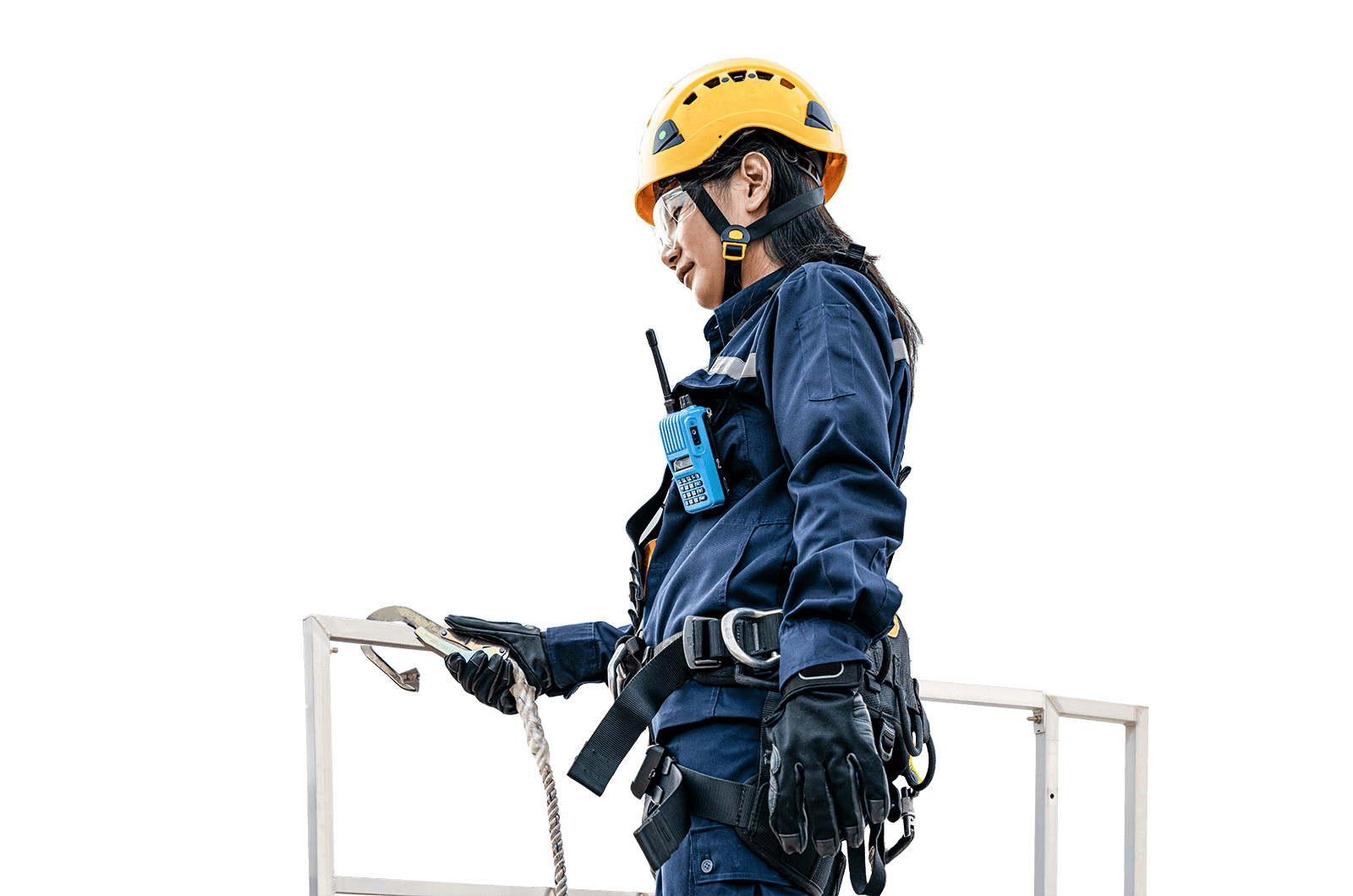