Immersion Ultrasonic Testing is used for the detection of sub-surface irregularities and flaws.
Immersion ultrasonic testing, offered at our Derby, England location, is an advanced form of ultrasonic testing, and is a more effective method of inspecting than manual ultrasonic testing. It offers improved Probability of Detection (POD) of the smallest defects, and can provide you with accurate reporting of the size and location of sub-surface irregularities and flaws in material or products.
In the highly specialised field of immersion ultrasonic testing, Intertek uses the latest in semi-automated and fully automated inspection systems and we have 12 immersion ultrasonic tanks at our UK-based UKAS and NADCAP accredited laboratory. Our NDT inspectors are PCN or NAS410/EN4179 level 2 and 3 qualified, and are highly experienced in using this advanced non-destructive testing technique.
Intertek specialises in using immersion ultrasonic testing for the aerospace and power industries to inspect raw material and components such as rectilinear discs. However, the technique is also suitable for use in other industrial or manufacturing sectors.
Typically with conventional ultrasonic testing, a couplant such as oil, gel or water is used on the tested item so that the transmission of the ultrasonic waves is more efficient and the transducer is manually moved over the tested item. With immersion ultrasonic testing, the tested part material and transducer are submersed typically in water and this allows for better sound travel from the transducer while maintaining consistent distance from the component. We can produce real-time and post-scan data processing and provide 'A', 'B' or 'C' scan imaging on metallic or composite products. This allows us to detect defect indications to the most stringent industry standards.
Intertek’s immersion ultrasonic testing capabilities can help you to ensure your products and components are safe and reliable, and will meet the high standards required for today’s markets. Our round-the-clock testing and speedy turnaround times means you can have the Total Quality Assurance that your production schedules will be met, with the minimum disruption to your processes.
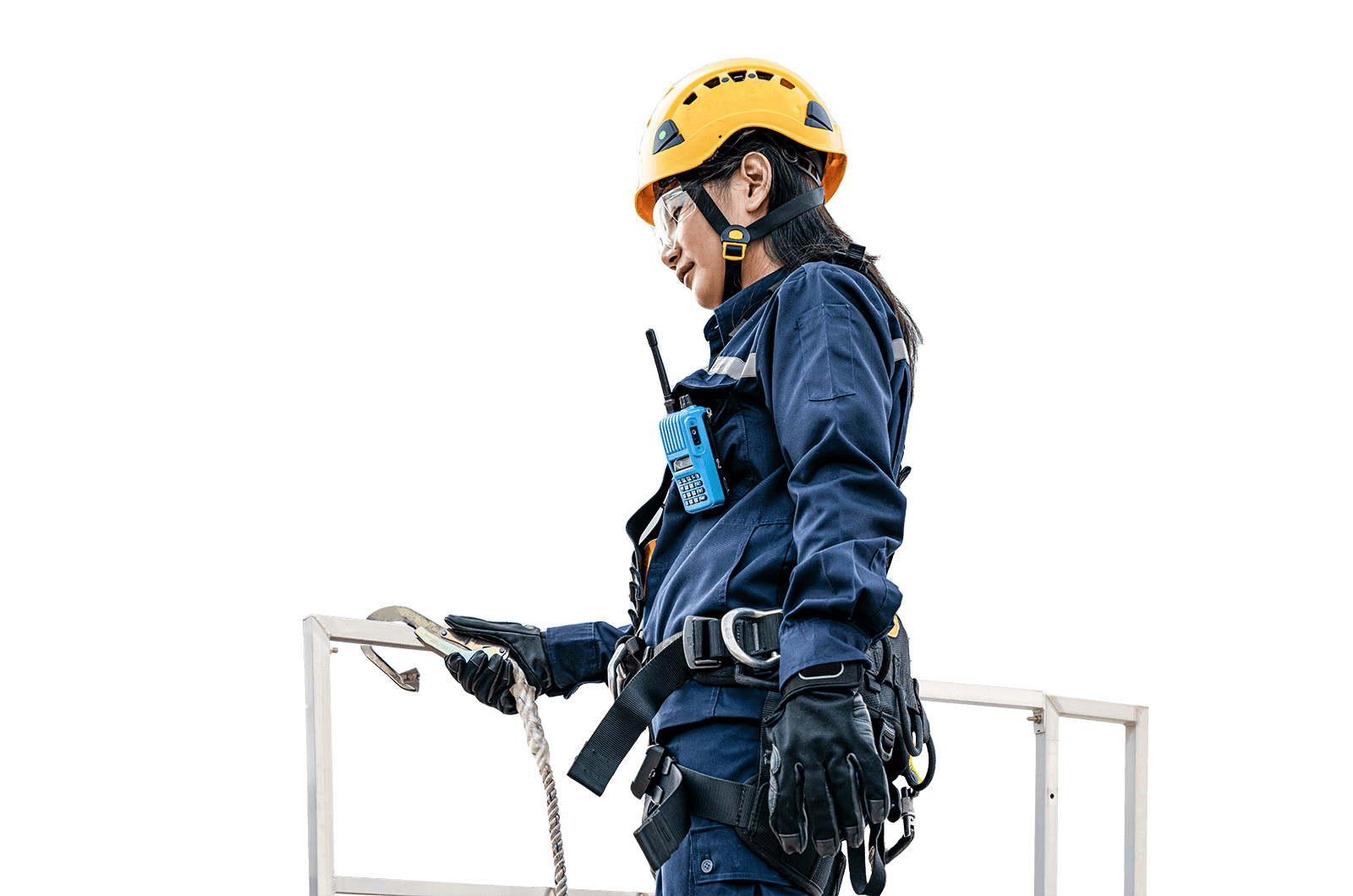