A Division Engineered to Build Better
Intertek's Building and Construction division is a suite of Intertek brands that are industry leaders across multiple architecture, engineering and construction disciplines, developing the most innovative product and project solutions.
Our experienced staff and comprehensive range of product-related testing and certification capabilities ensures that our clients have a clearly defined path to market, with cost-effective solutions and the ability to operate with pace and precision. Intertek's project-related assurance, testing, inspection and consulting services are the risk management and quality assurance partner you need to ensure the reliability, safety and performance of your new developments, existing assets and facilities.
Building Products
Building Projects
Knowledge Center
Building Health & Wellness: An Overview of Services
Acoustical Testing & Consulting Resources
Remote Pre Inspections for NFPA 80 / 101
Protek - Safety. Everywhere. Every Day
Fire Doors 101: Your Guide to Testing and Certification - Webinar Recording
Tornado Testing & Certification Requirements - Webinar Recording
Plumbing Products Testing & Certification - Webinar Recording
The Evolving Code Evaluation Process White Paper
Proposition 65 & the Furniture Industry Webinar Recording
Why Planning for FCC Certification is Key to Success in the Door Hardware Industry White Paper
Resources
- Search and Buy Building & Construction Standards
- SpecDirect
- Building Products Directory
- Project Connect (formerly myATI) – B&C Products
- Construction Hive – B&C Projects (PSIQest)
- My TestCentral
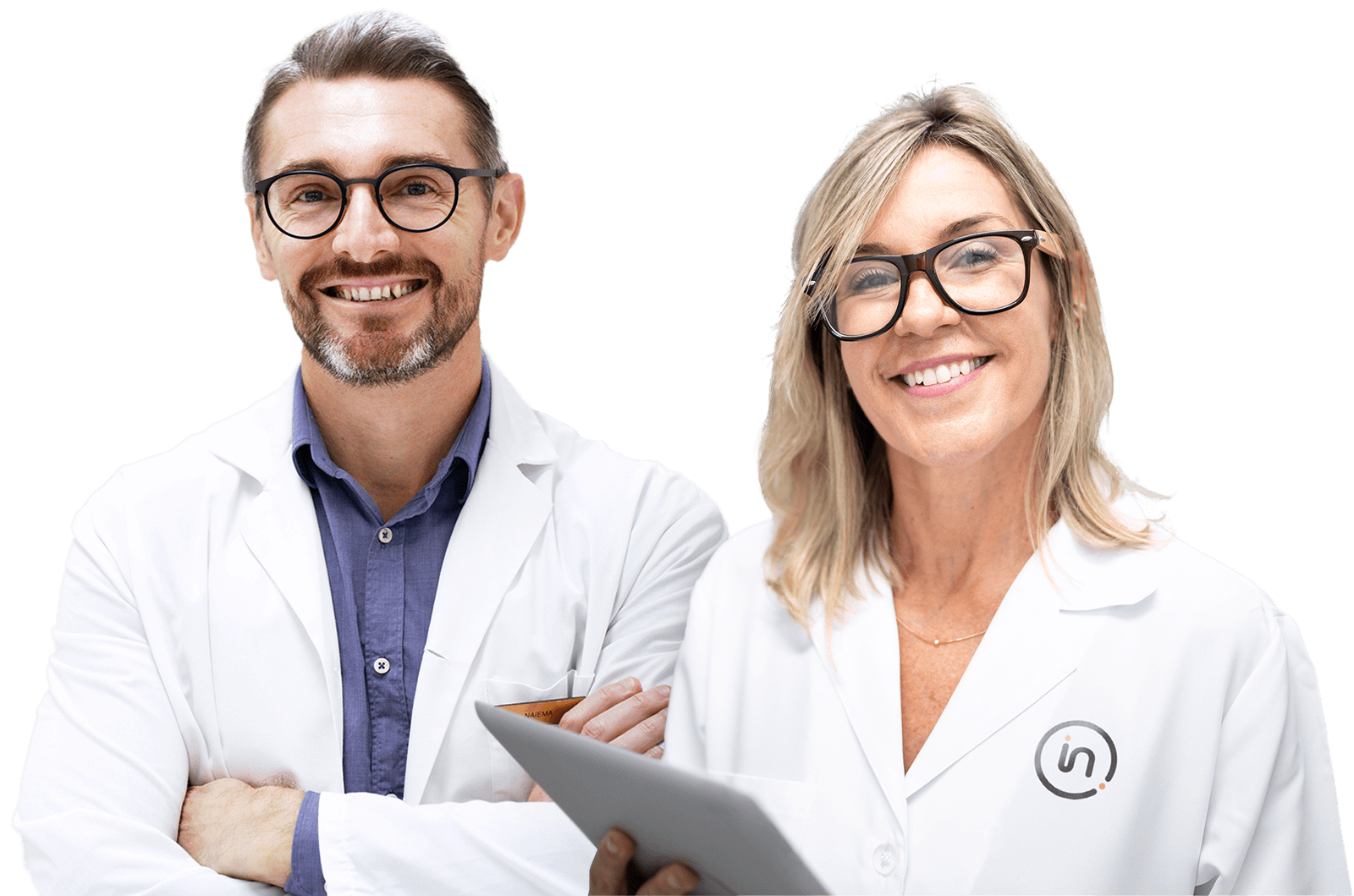