Smart Audits
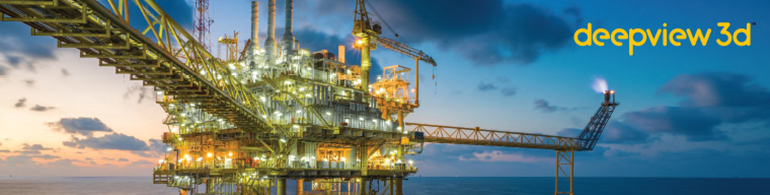
07 Jan 2020
Advanced Digital Integrity Solutions
Auditing a rig, plant, or unit must have a specific purpose and objective. Generally, audits are benchmarked by standards and regulations or by company specific key performance indicators (KPI). The results of an audit can vary from compliance to different levels of non-conformance or improvement opportunities. If the audit goal is production and maintenance optimization or continuous improvement then there are many different categories or elements that should be considered regarding quality and reliability. These elements are divided into two main subcategories: Processes & Systems and Physical Asset Condition.
In the assessment of Processes & Systems, it is important to identify the top critical bottlenecks or inefficient practices, so an appropriate tool, such as TPM, Lean, TQM, or Six Sigma, can be prescribed. The most interesting evaluated areas are usually those related with leadership and strategy, and if disconnects are identified here during the audit, the rest of the categories will likely reflect inconsistencies or poor performances as well. During a series of interviews, the directors, managers, and supervisors will demand plant optimization, production effectiveness, and overall uptime. But if planning and control strategies are not properly designed and implemented at this level, then the rest of the productivity edifice will, at its best, execute inefficient workflows that are constantly changed due to undesirable results.
The first goal of auditing Physical Assets is identifying the stakeholders' understanding of their own equipment condition and the relationship of the same to functional failures, failure modes, consequences of failure, and root causes. This will allow for improved corrective action initiatives and preventive maintenance plans. The second goal is the verification process that depends on the reliability of equipment information and the existence or location of the asset. The amount of inaccurate data related to equipment found during these audits is not too surprising. For example, in the oil and gas industry, production platform and exploration rig operators are trying to optimize their operating costs by revising maintenance plans. More importantly they are conducting extensive audits as a result of inexistent reliable data within their computerized maintenance management systems (CMMS). Audits are also a good principle for planning maintenance turnarounds. One of the most important strategies of turnaround planning is corrective maintenance (not emergency or contingency maintenance). Turnaround specialists should have a total knowledge of asset integrity (performance, condition, and location) so as to design risk matrices that combine equipment reliability efforts with cost-effective business decisions.
Today, new and advanced technology supports audits and turnarounds by creating baselines and providing objective reports on the condition and location of equipment in comparison with CMMS data, original equipment manufacturer (OEM) tolerances or original drawings.
- Laser scanning technology can recognize physical assets as well as create and validate piping and instrumentation diagrams (P&ID) or isometric drawings.
- Additionally, metrology can provide accurate information about dimensional changes, wear, and other conditions.
Intertek's Advanced Digital Integrity Solutions support audits with a combination of 3D laser scanning, phase array and metrology. Furthermore, light form modeler (LFM) software and dimensional control surveys can also provide highly accurate as-built 3D data on new or existing equipment. These are often used to generate 3D models and digital twins which validate information for regulatory requirements, business decisions, reliability assessments and predictive analyses. Intertek's Asset Integrity Management (AIM) specialists ensure that leadership, production, and maintenance groups are engaged during the Smart Audits to create a partnership environment. This collective approach promotes knowledge sharing and communication which in turn produces efficient and more accurate end results.
To learn more about Intertek's Advanced Digital Integrity Solutions, please visit intertek.com/deepview.
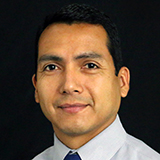
Rene Canales,
Sr. Reliability & Systems Engineer, Digital Solutions Specialist
Mr. Canales is a Reliability and Systems Engineer with more than 10 years of experience in the Oil and Gas, Energy, and Aerospace industries. In addition to his background of successful experience in reliability, he has spent years in digital asset management and real time operations of deep-water exploration, Blowout Preventers (BOP), and NASA Space Operations. His professional experience has been successfully attained in the areas of Asset Integrity Management (AIM), Total Productive Maintenance (TPM), Reliability Centered Maintenance (RCM), Root Cause Failure Analysis (RCFA), Failure Mode and Effects Analysis (FMEA), and Real-Time Data Analytics.