Verification of Part Cleanliness
13 Apr 2021
Helping you maintain cleanliness
Why worry about part cleanliness?
Cleanliness is key for components that will be sealed away for years during their service life. Even the most high-tech manufacturing process will generate debris and residues that need to be removed before being dispatched and environmental contamination is an ever-present risk. If not removed, this can lead to premature physical damage, blockages and corrosion.
No industry epitomises this better than the construction of nuclear reactors where exchanging a faulty part after installation can be extremely expensive and disruptive. Other industries such as aerospace and manufacturers of cryogenic equipment have also recognised the value of minimising the contamination present. Often the burden of proving the cleanliness of a part falls on the supplier and can be required at multiple stages of the process.
The challenges: Physical debris
The most visible kind of contamination is physical debris, which includes metallic swarf, blasting debris and fibres. International standards (e.g. ASTM F303 & BS EN ISO 23208) have been developed to look for this, each linked to dedicated industries with customer specific standards prevalent.
Intertek can work with you and your supply chain to demonstrate a chain of cleanliness from the first nut to final assembly with both on and off-site support.
Just finding debris is not always enough though – tracing the source of contamination is crucial to restarting production lines and tracing the root cause. Our range of instruments support this; from SEM-EDX to FT-IR, which can identify fragments, swarf and plastic contamination.
The challenges: Anionic contamination
Unlike physical debris, anion contamination is normally invisible to the naked eye and comes from residues left behind after processes and manual handling. Residues of halides (fluoride, chloride and bromide) are frequently prohibited due to their involvement in corrosion processes. Similarly, the presence of sulphate, nitrate, oxalate or phosphate can indicate the presence of residual chemicals following process treatments. Customer specific standards and specifications are more common in this area. Intertek's track record of collaboration with end users to develop processes that demonstrate compliance with customer specific specifications ranges from off-site support for component swabbing to whole component leaching.
The challenges: Avoiding cross contamination from consumables
To minimise the impact of a consumable transferring unwanted material onto an assembled part, customers can require chemical analysis on anything coming into contact with the part, from an abrasive wheel through to the sole of the worker's boots. Fluoride, chloride and sulphate are routinely tested for but the absence of low boiling point metals such as mercury can also be required. Intertek can offer chemical analysis of a wide variety of non-metallic materials tailored to suit your requirements.
Prove your process with Intertek
Our years of experience and state-of-the-art capabilities means we can tailor our services to help you prove your manufacturing processes from start to finish. From checking your cleaning process to final verification, we can help you every step of the way. Contact us today.
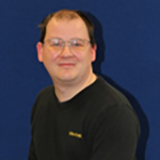
Stephen Gray, PhD. MChem,
Lead Development Chemist, Intertek Chemistry Laboratory, Derby, UK
Stephen Gray is the Lead Development Chemist for the Intertek Derby Chemistry laboratory in the Midlands. After being awarded a PhD in organic chemistry from the University of Leicester in 2011, he has been working for Intertek on a broad range of analytical and development projects alongside supporting the introduction of new analytical techniques.