Building Products Certification
26 Jan 2021
The Process & Benefits
What is building product certification? Why do it?
Testing and certifying products benefits manufacturers, architects, contractors and developers, giving them assurance that products meet safety and performance requirements.
Standards developed through consensus processes by Standards Development Organizations, or SDOs, designed to establish minimum safety and performance requirements. Building Codes adopt standards to establish minimum requirements for regulatory compliance and these codes are enforced by Authorities having Jurisdiction (AHJs). In most cases, manufacturers demonstrate compliance with the standards and codes through testing and certification.
Testing and certification is a multi-step process, typically having preliminary evaluation, testing, certification review and maintenance phases.
The project initiation phase includes client engagement and scope determination. The testing/certification needs of the product, its intended use and target markets are all considered. This information is used to create a test plan, where the lab determines what tests to do and how they will be done, as well as applicable engineering principles and confirmatory testing needs.
When products are tested for certification, the manufacturer's products are sampled by the certification body and are sent to the lab for evaluation. The manufacturing plant is audited to determine that standard manufacturing processes ensure the products are made in a manner consistent with the products submitted for testing. An engineer visits the manufacturing location to witness sample creation and document how the product is constructed. They also review quality control testing is and create a factory audit manual.
Next, the product samples are tested as detailed in the test plan. Test laboratories must be accredited to ISO/IEC Standard 17025.
Test data and certification documents such as the factory audit manual, evaluations and design listings are compiled in a listing report and sent for technical review, and an engineering review for verification of test data and other certification body requirements.
Once assembled, this data is submitted for a final certification review and for the certification decision.
Following an Initial Factory Audit, approved products are granted an Authorization to Mark. The manufacturer is provided with labeling procedures and guidelines on how the certification mark can be used. The listing report is then entered in the certification body's directory of certified products.
Maintenance of the certification includes regular follow-up inspections, typically unannounced, following procedures in the factory audit manual. Verification testing of selected products (determined during engineering review) may be required, and products may need to be reassessed if standards and codes are updated.
Certification benefits the entire construction industry, from manufacturers to contractors and developers to AHJs. Knowing products meet the requirements of relevant standards and building codes is important. Certified products signify quality, acceptance, and perception. And certification marks indicate an accredited independent third-party certification body has evaluated the product against appropriate standards and codes and maintains regular surveillance of manufacturing operations, providing greater peace of mind for all involved. Learn more in our webinar recording.
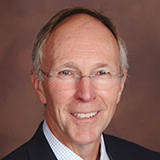
Michael Beaton,
Director of Special Projects
Michael Beaton is Director of Special Projects for Intertek's Building & Construction Certification group. With 35 years of industry experience in testing, inspection and certification, he provides technical support to the certification team and assists clients who are developing testing and certification programs.