TubeAlert Technology
15 Sep 2020
Predicting Early Life Creep Failures
Superheater and reheater tube failures are a leading cause of full forced outages in fossil fired power plants, and a leading failure mechanism in these systems is high temperature creep ruptures. Furnace tubes often operate near the upper temperature limit relative to their long-term stress-rupture properties. Creep failures occur due to localized high temperatures and localized wall thinning caused by erosion, high temperature oxidation, or corrosion. The localized high temperatures which cause creep failures will also form significantly thicker internal oxide scales than tubes operating at lower temperatures. These internal oxide scales can be measured nondestructively. TubeAlertSM is a technology developed by Intertek's Asset Integrity Management (AIM) division that uses nondestructive data collection and custom modeling to help avoid unexpected failures caused by long-term overheating in superheaters and reheaters
Long-term creep failures can normally be attributed to localized high temperatures. Virtually all boilers operate with some form of temperature distribution problem. Poor boiler design, operation at off-design conditions, burner-related problems, gas laning problems, etc. all contribute to nonuniform temperature distributions. Regardless of the cause, the result is that the tubing will suffer accelerated creep damage accumulation and will eventually fail in regions where the hottest temperatures are present. These hot spots will have a significantly lower creep life than tubes operating at expected tube metal temperatures and will cause unexpected and early life failures. The temperature distribution is not random, and a pattern can typically be found where only a handful of tubes are at risk of failure. Accurate and reliable condition assessment of these circuits is of paramount importance because of the high cost of unscheduled outages.
A TubeAlert condition assessment typically consists of two parts; on-site nondestructive measurements of internal oxide scales and wall thickness utilizing a propriety ultrasonic technique, and a remaining useful life (RUL) calculation using both measured and client provided information. A photo of a typical on-site examination location can be seen in Figure 1.
Figure 1 – Typical ultrasonic examination location, grit blasted in preparation for measurements.
The examination and calculations will provide an effective metal temperature, tube wall thinning rate, and stress for every measurement location. Accurate calculation requires the following information:
- Steam pressure history
- Original and current tube geometry
- Current steamside oxide scale thickness
- Tube materials
The steam pressure and the tube geometry are used to determine the stress history of the tube. The steamside oxide scale is used to determine the effective temperature history of the tubes since oxide scale grows as a function of material, time, and temperature. These two results are compared with the creep-rupture behavior of the tube material in question to conduct the RUL analysis. The RUL estimates are obtained using the TUBELIFEIII software developed by Intertek AIM.
The information obtained from informed sampling and analysis is useful in a variety of ways. It can be used to optimize the life of a unit, evaluate changes in operating conditions, and provide information to make the most cost-effective run/repair/replace decisions. For example, after a complete header survey, Intertek AIM can quantify the impact on superheater and reheater life should a utility choose to increase or decrease outlet temperatures and/or pressures. The software can also be used to quantify the life benefits as well as the modest heat rate improvement seen by chemical cleanings. If a total replacement is required, the information obtained from the Intertek AIM RUL analysis can be used to redesign the tubing for any required lifetime using the most cost-effective materials. The steam temperature profiles can also be used to alter selective circuits for a more uniform temperature distribution across the unit.
Case Study (AIM 14128772-2-2):
In 2015 Intertek AIM performed a TubeAlert examination on the reheater of a plant which operated for approximately 100,000 hours since commissioning in 2000. The plant had never experienced a reheater tube failure, but the examination revealed a severe temperature distribution problem. This was likely due to boiler design and improper use of orifice plates, which caused a large pressure drop and steam starvation on one side of the boiler. Through TubeAlert assessment, Intertek AIM identified the nine hottest tube circuits (Elements 4 through 12) for immediate replacement with stainless steel and four individual tubes in the top of their elements in the convection pass which had exhausted their creep life. A graph of the temperature distribution resulting from the TUBELIFEIII software can be seen in Figure 2
Figure 2 – A graph of tube metal temperature produced with Intertek AIM's TUBELIFEIII software.
The plant replaced all tubes that TubeAlert analysis indicated had exhausted their creep life. Based on the assessment findings the plant also decided to replace the entire upper section of reheater with stainless steel over the course of several outages, prioritizing the hottest elements. As a result of these critical preventative actions, the plant has still not had a reheater tube failure directly associated with long term overheating. As an additional benefit of these actions the plant eliminated the majority of the oxide exfoliation that was causing significant solid particle erosion on the intermediate pressure turbine components. The plant has not had a problem with solid particle erosion since the initial nine elements were replaced with stainless steel. These type of direct and indirect operational uptime improvements and cost reductions are typical of a TubeAlert condition assessment.
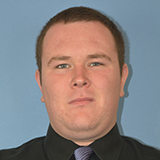
Colin Campbell, P.E.
Failure Analysis Laboratory Manager
Mr. Colin Campbell has experience in metallurgical engineering and field metallographic techniques. Over his career, he has completed a number of failure investigations in the petrochemical, power generation, and semiconductor industries. His field expertise includes failure investigations and root cause analyses, the preparation and evaluation of metallurgical replicas for assessing creep damage, ultrasonic measurement of internal oxide thickness in boiler tubes to assess remaining useful life, and multiple non-destructive inspection techniques for high energy piping.