A Closer Look at Field Evaluations & Labeling
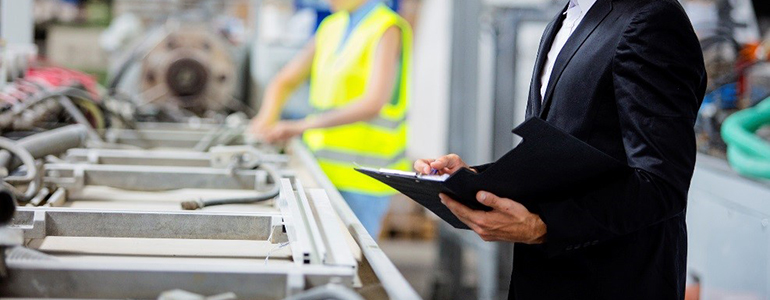
08 Jan 2019
How to Secure Local Approval to Get Your Products Operational
According to U.S. federal regulations, all electrical equipment in the workplace must be approved, identified, listed, or labeled by an OSHA-accredited nationally recognized testing laboratory (NRTL). If a local authority having jurisdiction (AHJ) finds installed equipment at a site they are inspecting does not bear the NRTL marks to show compliance with the appropriate electrical safety standards, the AHU could "red tag" the equipment, and taking it out of service. This could delay the occupancy of a building or business, proving to be costly for those involved. In some cases, a product may have not been listed by an NRTL due to labeling errors by the manufacturer or because the product certification process was not started early enough. In many cases, equipment imported to the U.S. from other countries has not been submitted to an NRTL for certification at all. In these cases, an urgent field evaluation can help get the project back on track.
Field evaluations allow for an on-site, non-destructive compliance assessment, and can also be used for one-of-a-kind, custom equipment or prototype equipment not intended to be mass produced. When equipment faces a "red tag" by the local authority, a field evaluation body (FEB) can be quickly dispatched to the site to address the issue. The FEB will send an expert to evaluate the installed equipment in question for risks related to shock, fire, and mechanical hazards. This is all done while taking in account the surrounding environment and those in contact with the product. In addition to a construction review and some non-destructive tests performed in the field, safety related markings, warnings, and safety features such as interlocks and emergency stops will be reviewed.
If, during a field evaluation, a product is found to be compliant with applicable requirements, the unit is labeled with the mark of the field evaluation body and a detailed report is issued, with the AHJ copied, to show the equipment as compliant. If a product is found to be non-compliant, a non-compliance report is issued that provides an explanation of each non-compliant issue. This information can be used as a guide for the customer as they determine what corrections are needed to comply. Once these corrections are made, the field evaluation body will request another site visit for a review of the fixes. If the corrections are found to be acceptable, the FEB evaluator will field label the equipment and issue the corresponding compliant report to the AHJ.
Field evaluations offer an opportunity to quickly solve problems with unlabeled equipment in the field. It is critical to follow all guidelines set forth by governing bodies when it comes to field evaluations and to be sure to use a field evaluation body approved by the AHJ in a specific jurisdiction. It is also important to understand that while preliminary inspections may be performed prior to equipment shipment, the equipment labeling associated with a compliant field evaluation is intended to be performed with the equipment installed in the field. The National Fire Protection Association standard NFPA 791 (Recommended Practice and Procedures for Unlabeled Electrical Equipment Evaluation) outlines this and is a good guide for understanding the process.
To learn more about field evaluations and field labeling, including insights on Intertek's services, check out our information page and resources.
This is the first in our new series on field evaluations and labeling. Stay tuned for more posts in the future.