Energy dispersive X-Ray (EDX) composition analysis, elemental mapping of a sample and image analysis supporting industrial investigational studies and chemical research
Energy Dispersive X-Ray Analysis, also referred to as EDS or EDAX, is an X-Ray technique used to identify the elemental composition of materials. Applications include materials and product research, troubleshooting, deformulation, and more.
EDX systems are attachments to Electron Microscopy instruments (Scanning Electron Microscopy (SEM) or Transmission Electron Microscopy (TEM)) instruments where the imaging capability of the microscope identifies the specimen of interest. The data generated by EDX analysis consist of spectra showing peaks corresponding to the elements making up the true composition of the sample being analysed. Elemental mapping of a sample and image analysis are also possible.
In a multi-technique approach EDX becomes very powerful, particularly in contamination analysis and industrial forensic science investigations. The technique can be qualitative, semi-quantitative, quantitative and also provide spatial distribution of elements through mapping. The EDX technique is non-destructive and specimens of interest can be examined in situ with little or no sample preparation.
In situations where combined Microscopy and EDX data acquired are insufficient to identify a specimen, complementary techniques are available, typically Infra-red (FTIR) Microscopy, RAMAN Microscopy, Nuclear Magnetic Resonance Spectroscopy (NMR) and Surface Analysis (X-ray photoelectron spectroscopy (XPS) or Time-of-Flight Secondary Ion Mass Spectrometry (SIMS)).
Intertek EDX analysis applications:
- Product deformulation and competitor analysis
- Adhesion, bonding, delamination investigations
- Optical appearance, haze and colour problems
- Disputed claim investigations and expert witness
- Failure investigations, identification of cause
- Catalyst quality, poisoning and elemental distribution
- Product imperfections and defect analysis
- Contamination detection, isolations and identification
- Quality control, raw material and end product
- Filler, pigment, fibre, additive distribution, orientation
- Assessment of plant particulate emissions
- Construction and maintenance monitoring (asbestos)
Benefits from EDX analysis:
- Improved quality control and process optimisation
- Rapid identification of contaminant and source
- Full control of environmental factors, emissions etc
- Greater on-site confidence, higher production yield
- Identifying the source of the problem in process chain
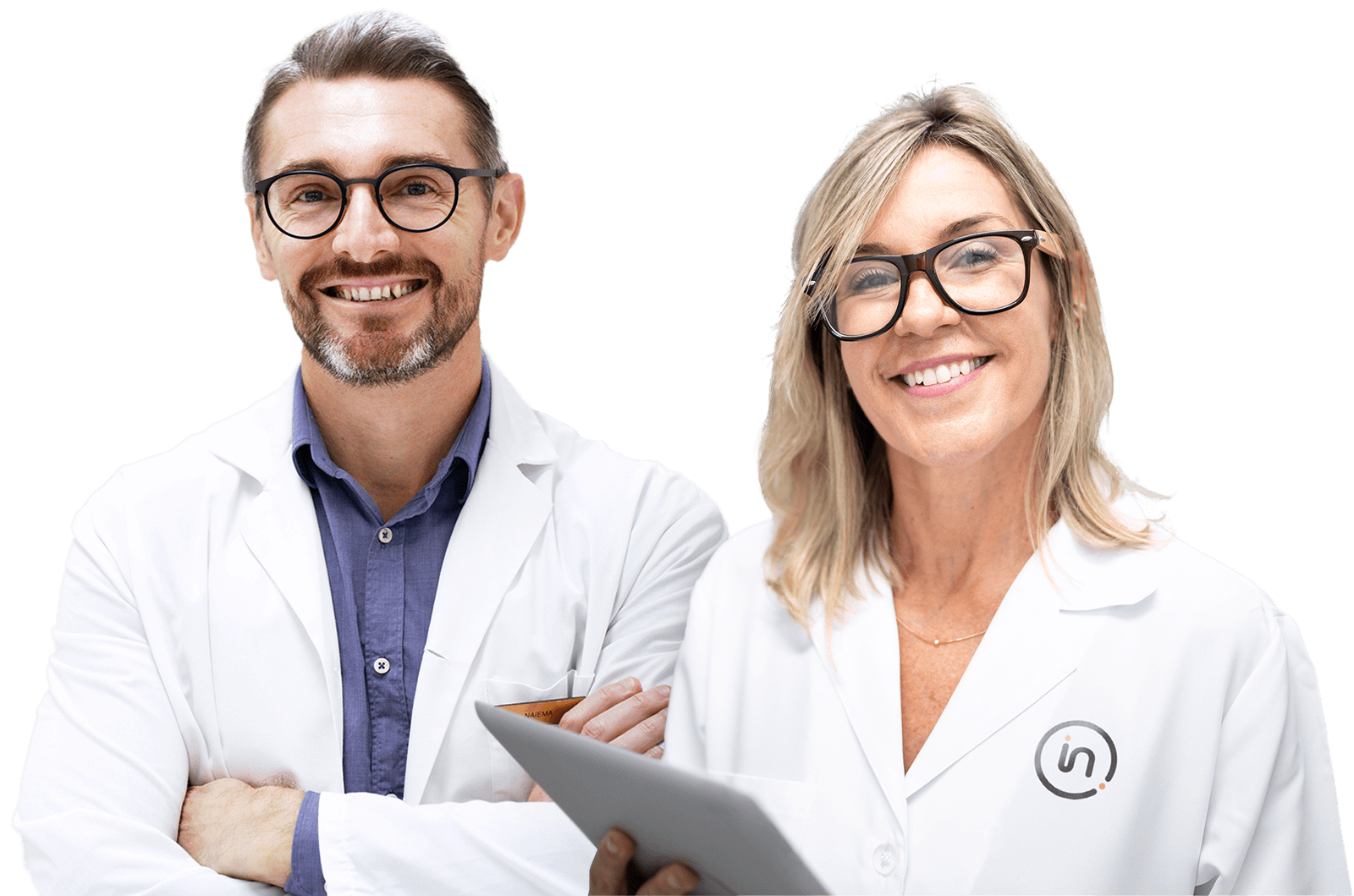