Intertek’s Global Semiconductor Safety Services (GS3) is a qualified evaluation service as required by SEMI S2
What is a SEMI S2 Evaluation?
The SEMI S2 document is a guideline intended to be used as a minimum set of performance-based environmental, health, and safety considerations. By being a guideline that is performance based it provides equipment manufacturers with the ability to use state of the art technology that the standards and guideline has not accounted for, but that provides equal to or better performance on the requirements.
A SEMI S2 evaluation performed by GS3 experts involves evaluating and testing the Semiconductor Manufacturing Equipment to all the applicable requirements and issuing a comprehensive report. The report is the key to end-user acceptance of your equipment. Acceptance of our evaluation reports is unparalleled, ensuring fast qualification of compliant requirements.
Exploring the Elements of SEMI S2
SEMI S2 was originally published in 1991 and the 0821 version is the most recent which was published August 2021. The guideline has 28 sections, 5 appendices, and 18 sections containing related information.
The guideline has requirements relating to:
- Documents provided to users (Section 9)
- Hazard Alert Labels (Section 10)
- Safety Interlock Systems (Section 11)
- Emergency Shutdown (Section 12)
- Electrical Design (Section 13)
- Fire Protection (Section 14)
- Process Liquid Heating Systems (Section 15)
- Ergonomics and Human Factors (Section 16)
- Hazardous Energy Isolation (Section 17)
- Mechanical Design (Section 18)
- Seismic Protection (Section 19)
- Automated material Handlers (Section 20)
- Environmental Considerations (Section 21)
- Exhaust Ventilation (Section 22)
- Chemicals (Section 23)
- Ionizing Radiation (Section 24)
- Non-Ionizing Radiation and Fields (Section 25)
- Lasers (Section 26)
- Sound Pressure Level (Section 27)
Demystifying the SEMI S2 Report
The SEMI S2 evaluation report is a comprehensive review of each requirement found within the SEMI S2 Guideline. Each requirement is stated with a corresponding observation by the GS3 expert. Typical product testing reports (such as IECEE test reports) have only 3 responses to each clause: Pass, Fail, or Not Applicable. For SEMI S2 reports there are 4 responses: ‘Conforms to the Stated Criteria’, ‘Conforms to the Performance Goal’, ‘Does Not Conform’, or Not Applicable.
Both ‘Conforms to stated Criteria’ and ‘Conforms to the Performance Goal’ are the equivalent as ‘Pass’. They differ in that Conforming to the performance goal allows a product to meet requirements by not specifically meeting the text of the standard. This allows for greater flexibility in accepting state-of-the-art technology as safe.
The SEMI S2 report is intended to be provided to the end user for their review and acceptance into their overall facility.
Request more information to see how Intertek can help your organization with SEMI S2 Testing.
Related Links
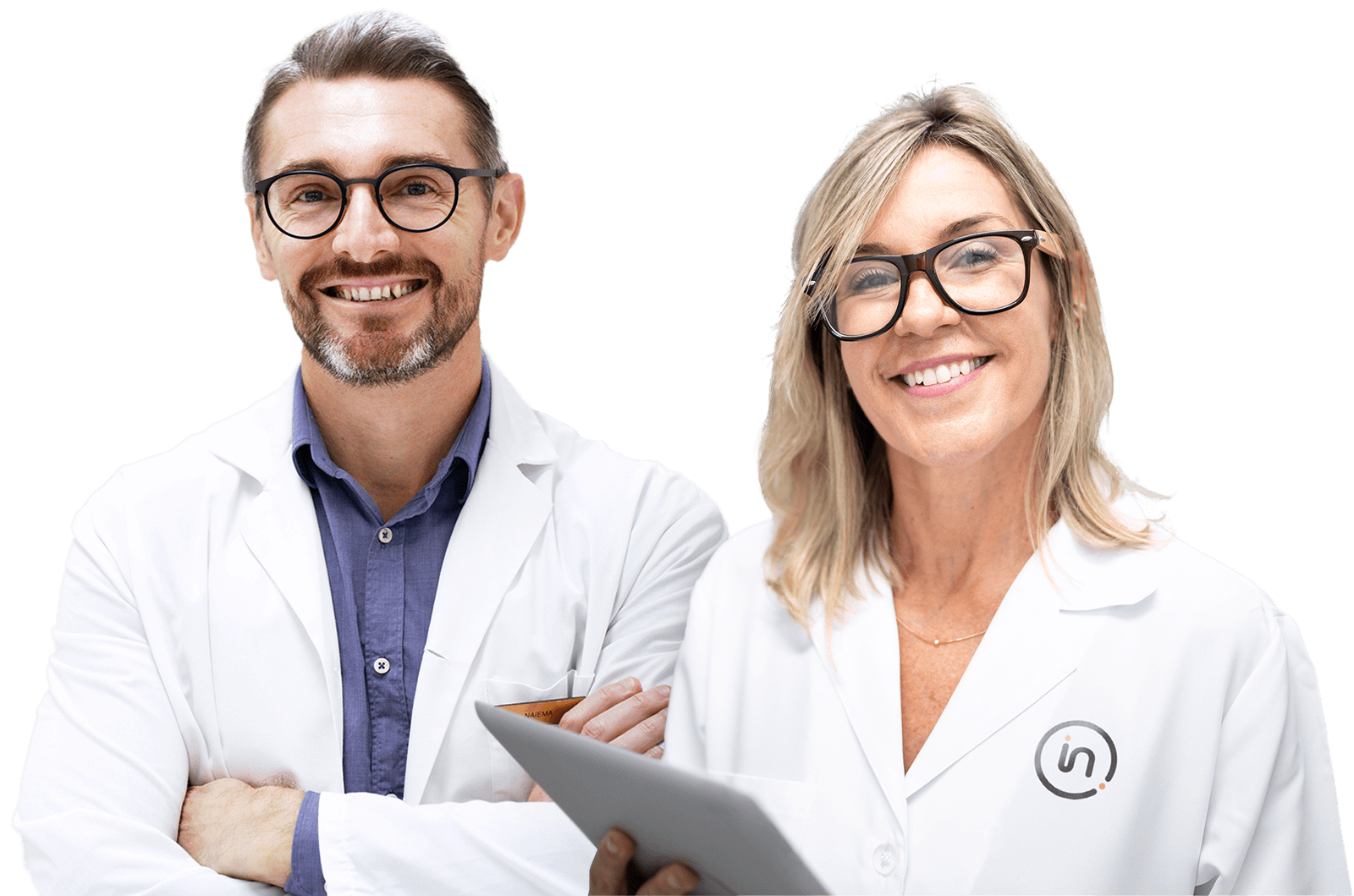