From product design and safety chain management to performance, safety assessments, and more. Functional Safety solutions to help you reduce risk and optimize your systems
What is Functional Safety?
Functional safety refers to the ability of a system or product to perform its intended function in a safe and reliable manner. It is concerned with the prevention of hazards caused by malfunctioning electronic or mechanical systems. functional safety is a crucial aspect of the design and implementation of systems and products, with the aim of ensuring their safe and reliable operation, even under abnormal conditions.
In functional safety, the goal is to minimize the risks associated with the use of a product or system, by ensuring that it functions correctly, even when things go wrong. This involves the identification of potential hazards, analysis of the risks associated with those hazards, and implementation of measures to mitigate those risks.
Functional safety is especially important in industries where there is a high risk of injury or damage, such as automotive, aerospace, medical devices, and industrial equipment.
Functional Safety: Overview and Methods White Paper
Benefits of Functional Safety
Every engineered system has risks: risks to people, risks to the environment, and risks to equipment and facilities. Functional safety is the planned reduction of those risks through automated safety systems. This involves a holistic analysis - evaluating all of a product’s systems as an entire working unit to determine how the product’s hardware and software interact and how the product responds to user inputs and the environment in which it is expected to function.
Functional Safety provides a number of benefits, including:
- The most obvious benefit of functional safety is increased safety. By ensuring that a product or system operates correctly, even under abnormal conditions, functional safety helps to reduce the risk of accidents, injuries, and fatalities.
- Functional safety also helps to reduce liability for manufacturers, designers, and operators of products and systems. By complying with safety standards and regulations, they can demonstrate that they have taken steps to ensure the safety of their products, which can help to reduce the risk of legal action.
- Functional safety standards require thorough testing and validation of systems, which can help to identify and eliminate potential defects and faults. This leads to improved reliability, as well as reduced downtime and maintenance costs.
- The rigorous processes and standards required for functional safety can help to improve the quality of a product or system, which can lead to improved customer satisfaction and brand reputation.
- Compliance with functional safety standards can also provide a competitive advantage for manufacturers and suppliers, as it demonstrates their commitment to safety and quality, which can be a differentiating factor in the marketplace.
Functional safety extends to the use of electronic and other types of systems to mitigate risk for a process, typically accomplished through equipment with sensory, logic, and acting elements. These systems can include calculations and analysis involving Performance Levels (PLs), Safety Integrity Levels (SILs), Failure Modes and Effects Analysis (FMEA), the IEC/EN 62061 and ISO 13849, IEC 61508 and IEC 61511 standards, and more.
Key Reasons to Implement Functional Safety
Functional Safety Standards
IEC 61508 — This is a general standard that provides a framework for functional safety across various industries and applications. It defines the concepts, processes, and requirements for achieving functional safety in electrical, electronic, and programmable electronic systems. The standard covers the entire lifecycle of a safety-related system and emphasizes the importance of risk assessment, safety integrity levels (SIL), and systematic safety processes.
ISO 26262 — This standard specifically addresses functional safety for automotive systems. It focuses on the development of safety-critical components and systems in the automotive industry, covering the entire product lifecycle from concept to disposal.
IEC 62304 — This is the standard that provides guidelines for the software lifecycle processes of medical device software. It specifies the requirements for the development, maintenance, and risk management of software used in medical devices. The standard covers the entire software development lifecycle, including software design, implementation, testing, and maintenance. It emphasizes the importance of software quality, risk analysis, verification, and validation activities to ensure the safety and effectiveness of medical device software. Compliance with IEC 62304 is crucial for medical device manufacturers to demonstrate regulatory compliance and ensure the reliability and safety of their software-based medical devices.
IEC 62061 — This is the standard that specifically addresses the functional safety of safety-related electrical, electronic, and programmable electronic control systems used in machinery applications. It provides guidelines for the design, development, implementation, and maintenance of these safety control systems. The standard emphasizes the use of a risk-based approach to determine the required safety performance level (PL) and specifies the necessary measures to achieve the defined safety requirements. IEC 62061 is widely utilized in industries such as manufacturing, automation, and process control to ensure the safe operation of machinery and equipment.
EN 50128 — This is a European standard that specifically focuses on the functional safety of software used in railway control and protection systems. It provides guidelines for the development of software-based systems, including requirements specification, design, implementation, verification, and maintenance. The standard emphasizes the importance of systematic and rigorous processes to achieve the necessary safety integrity levels (SIL) required for railway applications. EN 50128 covers various aspects of software development, including software architecture, coding standards, testing, configuration management, and documentation.
Intertek Functional Safety
Conformity Assessment Program & Mark Guidance
Intertek's Functional Safety Services
Intertek’s expertise in developing and guiding functional safety systems means we can assist in all stages. From product design to safety chain management to performance and safety assessments and more, we can help you reduce risk and optimize your systems.
Functional Safety is applicable to all industries and is increasingly in demand as manufacturers and end users look to further mitigate risk. Functional safety services can apply to:
- Companies/Designers/Inventors taking a product to specific markets
- Manufacturers looking to meet particular directives, requirements or recommendations from industry organizations, insurers, or regulatory bodies
- Product designers and businesses looking to ensure product safety
Industries include: industrial machinery, hazardous locations, appliances, medical, transportation, utilities, chemical, and more. Contact us to discuss the complete range of industries and products.
Related Services:
* Intertek does not provide consulting services for management systems certification. Any consulting activities provided by Intertek are separate and independent from certification activities.
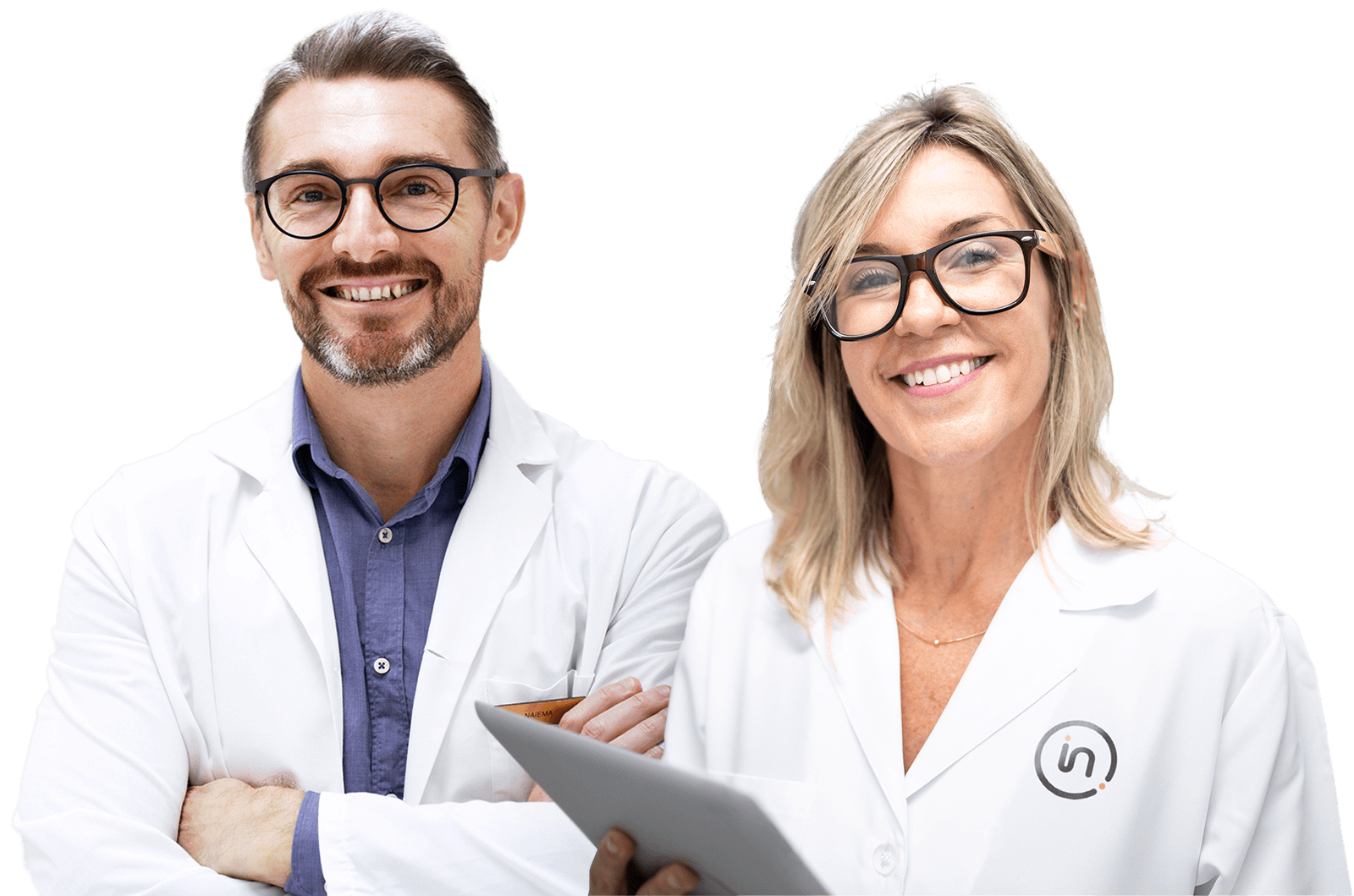