Glass delamination studies (USP <1660>) for pharmaceutical vials, syringes or drug bottle packaging including inner surface durability testing, screening analysis, studies of lamellae formation & data assessment
Glass delamination testing of pharmaceutical containers such as vials, ampules, cartridges or molded bottles are necessary to mitigate risks associated with quality and durability of the inner surface of the container and determination of lamellae formation (thin glass flakes). These studies help to evaluate the potential of a drug product to interact with and cause delamination and formation of glass particles.
Glass delamination represents a serious quality issue, and several drugs have recently been recalled due to this problem and regulatory authorities such as the US Food and Drug Administration (FDA) have highlighted these product recalls. Small glass particles - when injected directly into a patient - may lead to serious health risks such as embolic, thrombotic and other vascular events. High value drug products such as biopharmaceuticals typically use small-volume glass cartridges, vials, and prefillable syringes and so it is important to mitigate risks associated with appearance of lamellae and structural instability of the container.
Manufacturing process differences within the glass industry and the nature of drug product are reported to be the most dominant factors that affect glass delamination. Manufacturing conditions such as the molding process or formation from glass tubing under high temperatures, plus any additional treatments after formation, storage conditions and duration of storage processing operations at the pharmaceutical manufacturer (such as terminal sterilization by autoclaving) can all reduce the chemical resistance of glass. Various interactions can arise when products come in contact with glass surfaces including leaching, ion exchange, precipitation, glass dissolution and more.
Glass Delamination Expert Solutions
Our glass delamination specialists provide a range of solutions that help mitigate the risks associated with glass delamination for molded bottles, containers, vials or prefillable syringes. We provide laboratory services according to United States Pharmacopeia (USP) Chapter <1660>, ‘Evaluation of the Inner Surface Durability of Glass Containers’ to monitor ‘early stage’ indicators through predictive screening studies which begin with an assessment of the glass materials by applying the Surface Glass Test 660 (Type 1 glass). Aggressive screening conditions via a series of accelerated temperatures can be used to establish the chemical durability of different containers. This can help you to select the most chemically durable glass container or determine if changes in glass quality have occurred (e.g. between different batches). We also study the suitability of a given glass container for a specific product which involves determining the potential for lamellae formation with programs conducted over a suitable period of time with storage at elevated temperature conditions to stress the system.
Microscopy Investigations
Lamellae, due to their size, are difficult to detect by visual inspection. However, by using specialist microscopy techniques, we can perform tests to confirm product and glass quality. Our experts deploy light microscopy, followed by scanning electron microscopy (SEM) to inspect the size, shape and morphology of even sub visible particles that could have been released from the inner vial surface – a typical indication of delamination. Further examination into the nature of the particles is achieved with SEM - combined with energy-dispersive X-ray spectroscopy (EDX) to determine the elemental composition of detected particles and their origin.
SEM can also provide direct evidence that the glass and the liquid product are interacting by studying the appearance of inner vial surfaces. This data, together with advanced microscopy studies using differential interference contrast (DIC), can reveal a detailed picture of pitting and corrosion of the interior surface of a vial.
Ensuring a Safe Product and Glass Container Supply Chain
Our expertise helps you to ensure that patient safety and product quality are not compromised when a glass vial, cartridge, or syringe are used as primary packaging for your pharmaceutical product. Intertek's thought-leaders have over 20 years’ experience with pharmaceutical packaging materials, container closure systems and product development support and can assist you in minimising the risks associated with glass delamination. As part of your glass supply chain best practice, our expertise can help you to source high quality containers, monitor the quality on an ongoing basis and resolve instances of failure. Our teams can also assist you in detailed studies of potential contamination by glass packaging beyond glass delamination, including the study of metal ions leaching from glass, interaction with buffers and adsorption of drug molecules or formulation components on glass surfaces. Bringing quality and safety to life, we offer Total Quality Assurance expertise to help you to meet and exceed quality, safety and regulatory standards.
Our laboratories monitor the pH and the extracted elements in solution, in particular determining the concentration of silicon using inductively coupled plasma-optical emission spectroscopy (ICP-OES) or ICP-mass spectrometry techniques (ICP-MS). The presence of a higher amount of glass ions (e.g. Si, Al, B) including increases in Si concentration, the ratio of Si/O or Si/Al, in the test solutions. These are indicative of loss of glass durability or onset of glass delamination which may lead to formation of particulate matter or glass flakes.
We can conduct these studies with model systems but can also perform with the drug product liquid stored in the glass container. This helps to assess the propensity of a pharmaceutical liquid to react with its primary glass container.
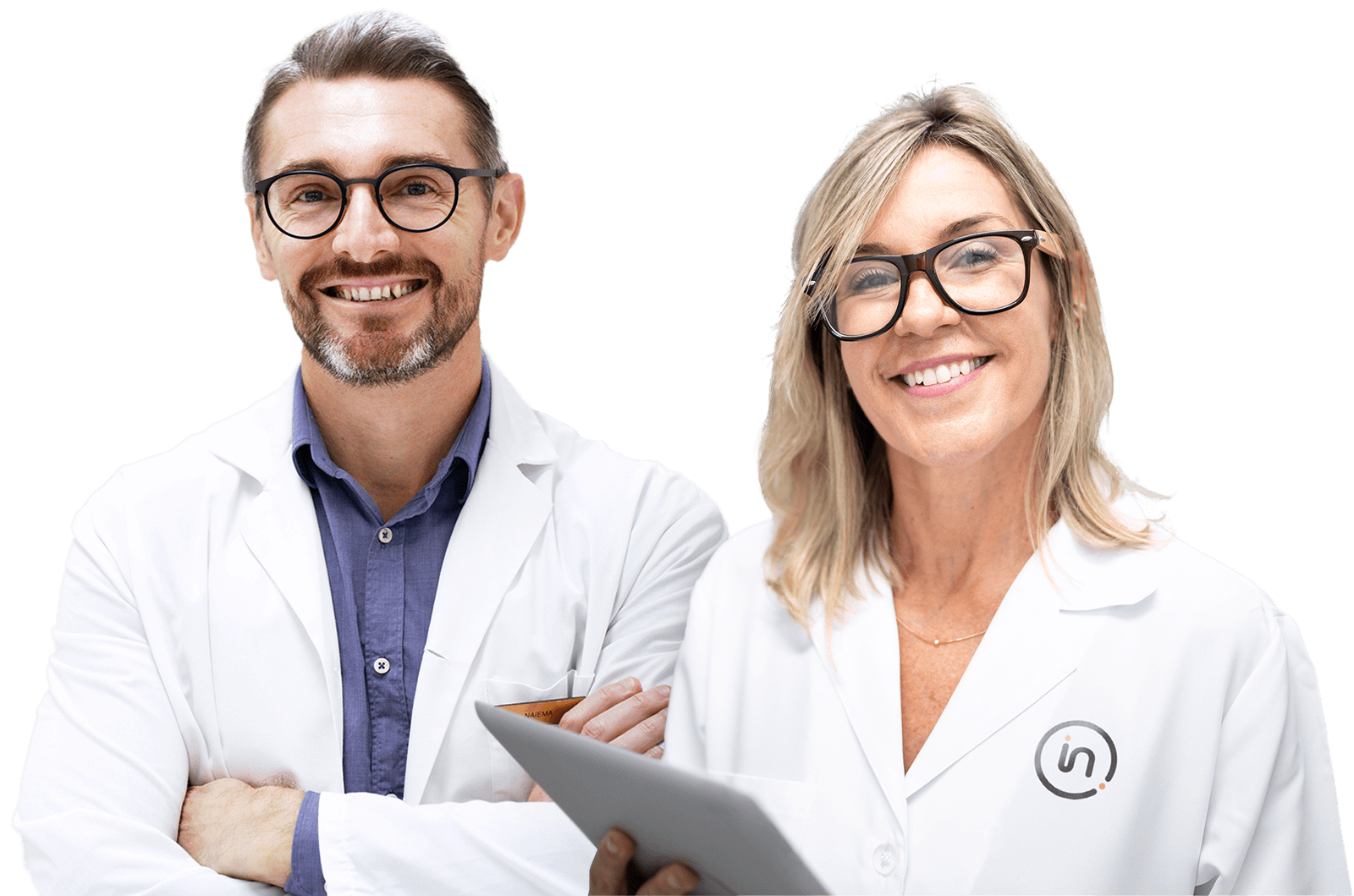