Specialist inhalation drug product testing services including particle size and droplet characterization, delivered dose testing and aerodynamic particle size analysis for pressurized metered dose inhalers (pMDI), dry powder inhalers (DPI), nebulizers or soft mist inhalers
Inhalation drug product testing is a vital aspect of orally inhaled or nasal drug product (OINDP) development, driving insight into the pharmaceutical characteristics and the formulation/delivery device relationship.
Specialist inhaled pharmaceutical product analysis and testing techniques, performed under controlled conditions and in line with established and robust methods, are essential to characterise the drug product. Critical quality attributes (CQAs) can be established and from these tests, and the performance of the formulation, together with a specific device can be assessed. This inhalation testing is required throughout the development cycle from testing early-stage candidate formulations to device screening, to formal stability studies and finally through to commercial batch release.
There are various guidance documents from the CDER (FDA) and the EMEA that outline the testing that is required as part of your Chemistry Manufacturing and Controls (CMC) package. These are in place to ensure continuing drug product quality and performance characteristics when developing both novel inhaled drug products and also abbreviated drug applications for generic products. The documents provide guidance on the specific analytical tests and the appropriate body of analytical test data required. This information is then used to confirm release specifications for both clinical batches and commercial batches, as well as inform the Summary of Product Characteristics (SmPC) and finally the Patient Information Leaflet (PIL). Testing should be performed all the way through development (in line with a QbD approach) and detailed specifications should be established before any clinical work.
In-vitro bioequivalence (IV-BE) studies are required for generic developments and are also based on these same analytical tests, with defined packages of work scoped out across numerous product-specific guidance’s (FDA).
Inhalation Drug Product Testing Services
Our Good Manufacturing Practice (GMP) compliant inhalation drug product testing is conducted by experts in programmable temperature and humidity-controlled laboratories according to guidance documents from regulatory authorities (CDER (FDA), EMEA). We support inhalation drug product development for a wide range of products such as pressurized metered dose inhalers (pMDI), dry powder inhalers (DPI), nebulizers, nasal sprays or soft mist inhalers. These classes of OINDP have very different mechanisms of action and formulations and we ensure that the most suitable testing requirements are deployed.
We are adept at method development & validation, product performance testing, chemical assay/impurities content, physical characterisation and, determination of moisture content. We routinely conduct accelerated and real-time stability studies to support clinical and commercial batch shelf life, as well as early stage formulation feasibility. With over 30 years of experience in OINDP development, we have built a reputation for providing outstanding customer service for challenging pharmaceutical developments programs. We generate robust and accurate data for OINDPs, under controlled conditions with established methods and experienced analysts offering a truly flexible and expert resource in inhalation product testing and development support which includes strategies for rapid repurposing for inhaled administration routes.
With specialist capabilities in development and testing of inhaled biologics, our scientists deploy strategic programmes of orthogonal analytical methods which aim to fully characterise the biologic and to establish whether the inhalation device delivery mechanism has impacted critical parameters such as the biologic's structure, purity (aggregation, degradation, etc) and the activity in line with the ICH Q6B Guidance.
It is necessary to characterise the dose delivered. The delivered dose should be consistent with the label claim, have low batch to batch variation and must be stable through-life (for example, for a multi-unit dose product, it is necessary to confirm that actuation 1 is the same as actuation 100).
Our scientists are knowledgeable in the testing regimes required for success. We deploy the most suitable apparatus for pMDI, DPI, soft mist or nebuliser products using robust methodology conducted in a controlled environment for testing to achieve accurate and reliable data.
Spray pattern and plume geometry characterisation during development is a regulatory requirement for pMDI and nasal spray products aimed at the US market (with the majority of European developers also including this information in their submissions). Spray pattern data is also required for release testing.
The shape, angle and duration of plume is highly influential in the uniform delivery and bioavailability of the product, and therefore product efficacy. For a nasal spray, for example, the shape of the plume and how disperse it is will effect where the drug product is it deposited in the nose and this in turn affects absorbance and bioavailability. Our scientists use automated actuation and analysis by instruments such as the Proveris SprayView which incorporates actuation and high-speed imaging to obtain accurate and robust data that enables you to calculate various parameters.
ON DEMAND WEBINARS
Repurposing Products for Inhaled Delivery - Rapid Response Strategies
Formulation and Manufacturing Approaches for Nasal Drug Products
ARTICLE DOWNLOADS
Repurposing Vaccines for Intranasal Development
In Vitro Bioequivalence for Pulmonary and Nasal Delivery
Nebulised Drug Development Considerations
Assessment of Foreign Particulate Matter in DPI Formulations
Pharmaceutical News & Events
- PRESS RELEASE: Lab expansion to enhance capabilities in inhaled biologics drug development
- PRESS RELEASE: Intertek partners with CrystecPharma to advance formulation science and accelerate development for dry powder inhalers
- NEW! Blog: Optimising Quality in Pharma Supply Chains
- Determination of Particles in Pharmaceuticals - Article
- Discover our Audit Live Tool for direct access to our scheduled audits
- Extractables/Leachables Lab Tour - Request access
- Medical Device Extractables & Leachables Studies
- Glycosylation Analytical Approaches for Antibody Therapeutics
- Rapid Determination of Low/Trace Level Benzene in Pharmaceutical Excipients and Finished Products
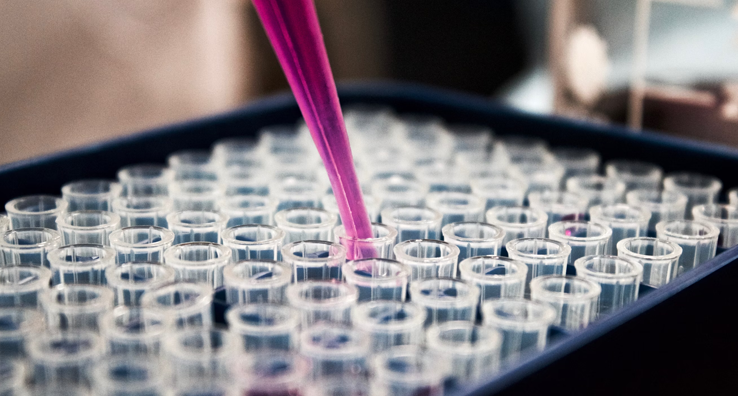
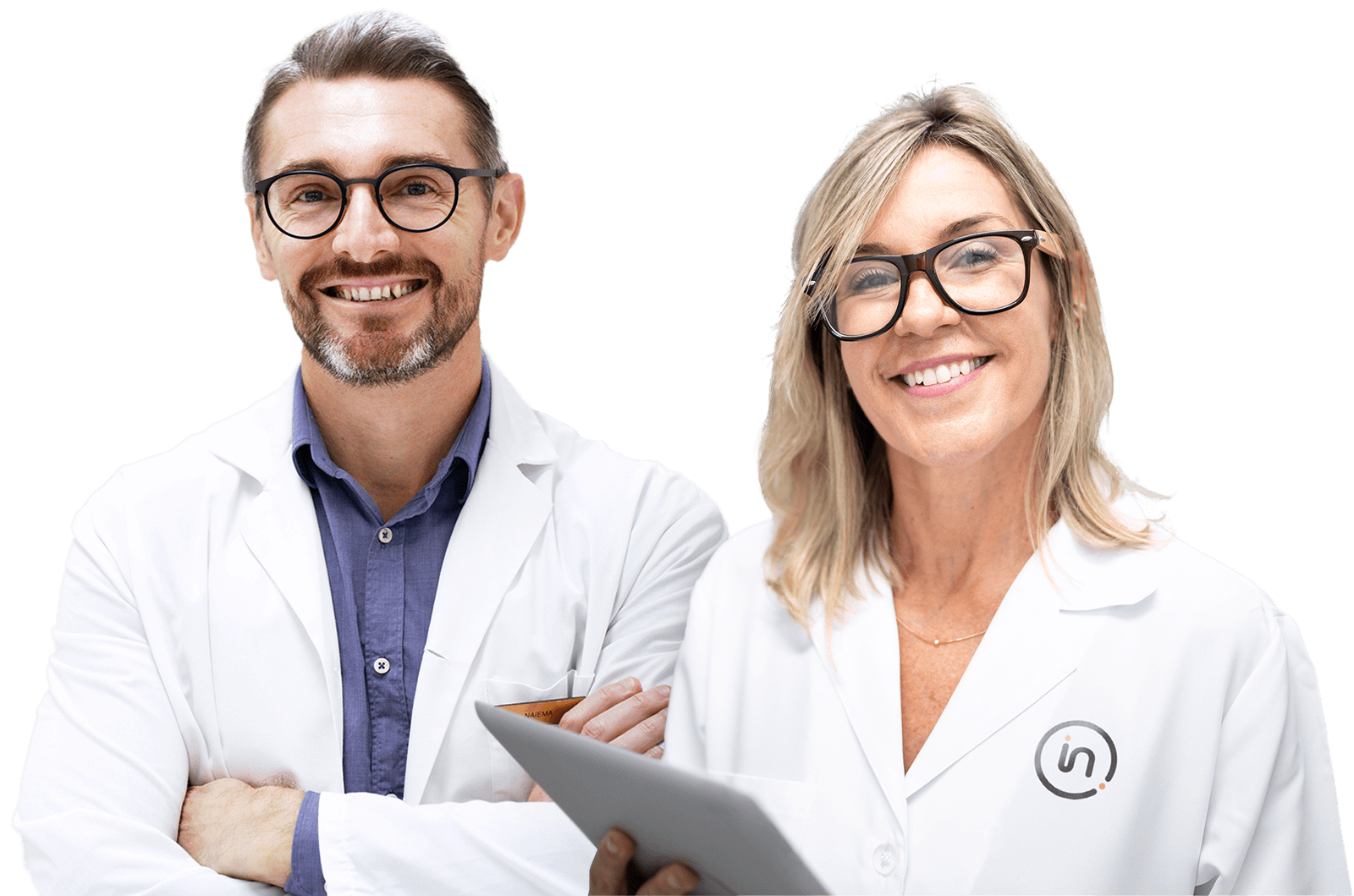