From product conception and design to manufacturing and distribution, potential hazards exist throughout the business process.
Many companies search for ways to eliminate international technical trade barriers and minimize potential risk, while proactively managing the whole supply chain in order to maintain their competitiveness in the marketplace. Establishing a total quality control system along the whole manufacturing process has become a necessity for many companies.
Intertek’s Total Quality Assurance (TQA) service provides an integrated, systematic approach to ensuring that customers and suppliers alike have an effective and sound quality system in place. TQA goes beyond just product safety requirements to actually accelerate time-to-market, improve product quality and reduce overall costs.
Related services to TQA include:
- Quality System Evaluation - Provides an extensive review of the quality of a factory’s existing system management, implementation of standards, procurements and current manufacturing procedures.
- TQA System Set Up - Offers advice on ways to fully utilize corporate resources and improve upon the whole production system. In addition, it applies preventative and corrective measures to establish defined and detailed traceability systems, from raw material procurements to marketing of the products.
- Systematic Records of Production Information - Documents and records production information in Intertek’s extensive database at every point of the manufacturing process. The collected data includes related equipment and material performance, process inspection, safety standards and compliance information.
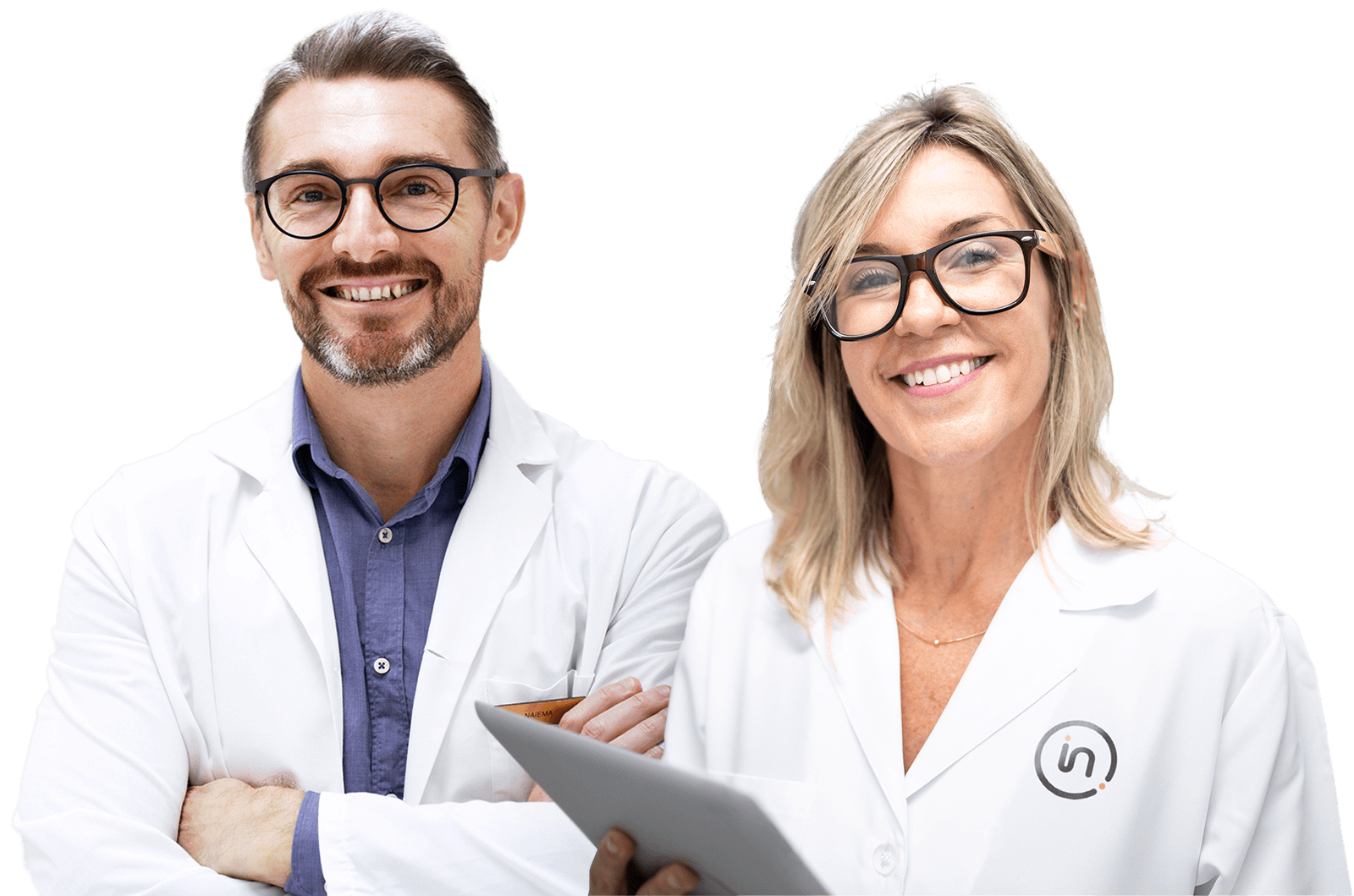