Adhesive testing to determine performance and properties across multiple industry applications such as aerospace, automotive, construction, packaging, industrial, medical and energy using using various adhesive testing methods to support application development and quality assurance
Adhesive testing is necessary to evaluate the long-term reliability and durability of adhesive products in various applications. Advanced adhesives are now available for a wide range of industries, including building products, aerospace, automotive, and packaging. For each new application you encounter, each new substrate (e.g., foils, paper, textiles, metals, foam, plastic, rubber, or glass) you consider, a customised adhesive product is likely required to meet the specific physical demands of the bonded joint and the stability requirements of the product in use.
Adhesives can be challenging to evaluate due to their variety, chemistries, and curing processes. Accordingly, a multidisciplinary approach with various adhesive testing methods can be required, encompassing aspects such as the physical properties of adhesives, study of adhesive strength and interfaces and performance under specific environmental conidtions. Relevant adhesive test methods and stringent testing procedures can provide assurance against failure, which can occur due to incorrect resin or additive selection, inadequate amounts and curing, contamination issues, cross-contamination issues, substrate issues, or formulation issues. This testing also plays a key role in production quality assurance and helps troubleshoot quality issues.
Our experts produce fast and accurate performance adhesive test data for products used in various industries and applications, such as aerospace, automotive, and construction. The data we provide assists material engineers in the selection of materials in global markets. It includes adhesive strength testing such as tensile, shear, and peel data, as well as other adhesive property tests (e.g., impact, odor, electrical properties and hardness). Testing can be performed in hot/wet/dry conditions at ambient, elevated, or sub-ambient temperatures. We can also provide studies testing before and after accelerated storage, during or after thermal cycling, weathering or stress by cataplasm storage or within a re-life protocol. Additionally, we provide testing of coatings, chemical analysis and development support testing, quality assurance programs, and troubleshooting analysis investigations.
What adhesives tests support formulation development?
Our adhesive formulation testing experts analyze adhesives across a wide range of applications, from packaging to transportation to the electronics industry. They have experience across a wide range of curing processes (heat-activated curing adhesives, UV-activated curing adhesives, anaerobic adhesives, moisture-activated, and pressure-sensitive adhesives) and chemistries (epoxies, urethanes, polyimides, acrylics, cyanoacrylates, silicones). We deliver both chemical testing and physical performance testing as tailored programs to meet your specific needs.
We support the development of new adhesive formulations through performance testing, including adhesion, peel, lap shear strength, shear modulus, tensile, flexural, impact, and cleavage strength, durability, environmental resistance, conductivity, and other mechanical properties, such as static shear, dynamic shear, creep resistance and fatigue. We also analyse physical attributes (softening point, rheology, viscosity, pot-life, density, solids content, filler content, specific gravity, and colour) and chemical analysis to gain in-depth understanding of the complex formulation components, their interactions, physical properties, long-term stability, relevant bonding, and aging processes, and an understanding of the processes that occur between the adhesive and the substrate interface. The thermal performance of adhesives and coatings canbe analysed using Coefficient of Linear Thermal Expansion (CLTE) using Thermomechanical Analysis(TMA), Dynamic Mechanical Analysis (DMA), Thermogravimetric analysis (TGA) and Differential scanning calorimetry (DSC). Techniques such as DSC or TGA are employed to study changes in physical properties that can occur during the curing process. We also perform accelerated aging tests and determine the rate of cure as part of the overall assessment to establish durability.
Adhesive Quality Assurance Programs
We tailor quality assurance programs for your adhesive chemistries or curing processes to evaluate the critical attributes and fundamental properties of ongoing production batches, ensuring they meet specifications and supporting sourcing by monitoring the quality of incoming materials. Our QA programs typically include the collection of data to enable product and process performance, driving insight through the use of Statistical Process Control tools.
Troubleshooting Performance or Quality Issues
To solve adhesive quality issues, we apply a wide range of spectroscopy (FTIR, RAMAN, RAMAN microscopy), microscopy (optical, scanning electron microscopy), chromatography (GC-MS, HS-GC), and mass spectrometry alongside key performance tests such as lap shear or peel. These techniques are strategically applied to address issues such as integrity, mixing, consistency, and to ensure more control over a wide variety of potential future issues. Mass spectrometry (either MALDI-TOF or LC-MS) may be employed to yield information about the buildup of oligomers during curing. This can include bulk oligomers and the formation of low levels of adducts during mixing. We may also use techniques such as Differential Scanning Calorimetry (DSC) or Thermographic Analysis (TGA) to study changes in physical properties that can occur during the curing process.
Adhesives Strength Testing:
- Adhesive Peel Test or Stripping Strength of Adhesive Bonds (180 degree peel) ASTM D903
- Bond Strength / Ply Adhesion ASTM F904
- Climbing Drum Peel of Adhesives ASTM D1781
- Peel Adhesion ASTM D3330
- Peel Adhesion to Rigid Substrates ASTM D429
- T-Peel of Adhesives ASTM D1876
- Floating Roller Peel of Adhesives ASTM D3167
- Lap Shear Metals ASTM D1002
- Lap Shear Adhesively Bonded Plastics ASTM D3163
- Lap Shear Sandwich Joints ASTM D3164
- Lap Shear Adhesive Joints ASTM D3528
- Lap Shear Thick Adherend Metal ASTM D5656
- Lap Shear Adhesion for Fiber Reinforced Plastics ASTM D5868
- Tensile Adhesion Properties ASTM D1623
- Tensile Strength of Sandwich Constructions (Flatwise Tensile) ASTM C297
- Standard Test Method for Apparent Shear Strength of Single-Lap-Joint Adhesively Bonded Metal Specimens by Tension Loading (Metal-to-Metal) ASTM D1002
- Adhesives - Determination of Tensile Lap-Shear Strength of Rigid-to-Rigid Bonded Assemblies ISO 4587
- Adhesives - Wood adhesives for non-structural applications – determination of tensile shear strength of lap joints EN 205
- Adhesives - Determination of Tensile Lap-Shear Strength of Rigid-to-Rigid Bonded Assemblies EN 1465
- Adhesives - Peel test for a flexible-bonded-to-rigid test specimen assembly - Part 1 90° Peel ISO 8510-1
- Adhesives - Peel test for a flexible-bonded-to-rigid test specimen assembly - Part 2 180° Peel ISO 8510-2
- Adhesives - T-peel test for flexible-to-flexible bonded assemblies ISO 11339
- Peel Adhesion EN 1939
- Floating Roller Peel of Adhesive – ISO 4578
Additional Adhesive Tests:
- Exposure of Adhesives to Artificial Light (QUV) ASTM D904
- Determination of Odor of Adhesives ASTM D4339
- Moisture Conditioning ASTM D5229
- Pull-off Strength of Coatings using Portable Adhesion Testers ASTM D4541
- Pull-off Test for Adhesion ISO 4624
- ‘Loop’ Tack Measurement FINAT FTM9
- Peel Adhesion (180°) at 300 mm/min FINAT FTM1
- Peel Adhesion (900°) at 300 mm/min FINAT FTM2
- Self adhesive tapes - Determination of peel adhesion properties (180° & 90° Peel) ISO 29862
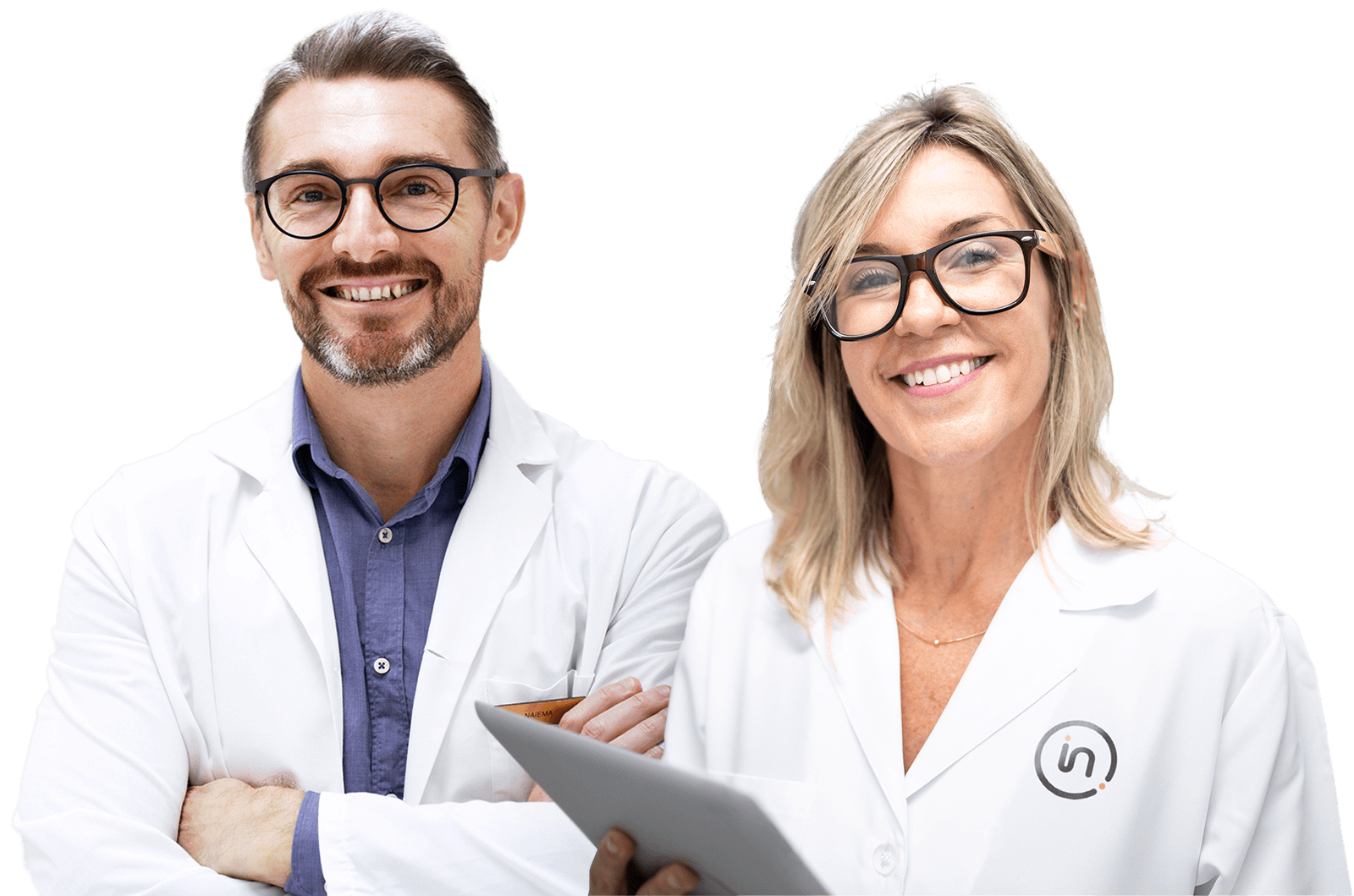