Effective October 2, 2015
Effective Date (see Schedule below): October 2, 2015
Impact Statement: A review of all Listing Reports is necessary to determine which products comply with new/revised requirements and which products will require re-evaluation. NOTE: Effective immediately, this revised standard will be exclusively used for evaluation of new products unless the Applicant requests in writing that current requirements be used along with their understanding that their listings will be withdrawn on Effective Date noted above, unless the product is found to comply with new/revised requirements.
Overview of Changes (Specific details of new/revised requirements are found in table below):
- Aligned impact test requirements for polymeric enclosures in damp locations.
- Aligned weatherometer and impact test requirements for polymeric enclosures in wet locations.
- Updated requirements for soldered connections.
- Expanded to include requirements for conduit closure plugs, knockouts, and twist-outs.
- Updated printed wiring boards requirements.
- Updated Abnormal and Leakage current tests procedure.
- Added new Knockout secureness and Thermal aging tests.
Schedule: So that shipping of products with Listing Marks will not be interrupted, an approximateschedule has been established to ensure Listing Reports are found compliant by Effective Date:
- February 6, 2015 = 8 Month Report Review – Intertek will review all Reports. Update if compliance is verified or issue Findings Letter/Quote for any re-evaluations needed
- April 1, 2015 = 6 Month Quote Cut-off – Quotes returned for necessary re-evaluations
- September 3, 2015 = 30 Day Warning – Client advised of all non-compliant Reports to be Suspended
- October 2, 2015 = Effective Date – ATM Suspended for all non-compliant Reports
Fees: An initial review of Listing Report (s) will be covered by a direct billing project and will be invoiced at not more than $1000 per report.
Client Action Required:
Information – To assist our Engineer with review of your Listing Reports, please submit technical information in response to the new/revised paragraphs noted in the attached or explain why these new/revised requirements do not apply to your product (s).
Current Listings Not Active? – Please immediately identify any current Listing Reports or products that are no longer active and should be removed from our records. We will do this at no charge as long as Intertek is notified in writing prior to the review of your reports.
NOTE: Additions to existing requirements are underlined and deletions are shown lined out below.
Clause | Verdict | Comment | ||||||||||||||||||
---|---|---|---|---|---|---|---|---|---|---|---|---|---|---|---|---|---|---|---|---|
6 | Info | Environmental Locations | ||||||||||||||||||
6.2 | Update Remark: Aligned impact test requirements for polymeric enclosures in damp locations. Clarification of Class 2 and LED Class 2 exemptions. A unit intended for damp locations shall be (a) subjected to the environmental tests specified in Clause 9.12 unless all live parts and traces on the printed wiring board are potted (see Clause 7.7) or conformal coated (see Clause 8.7.2); and b) if provided with a polymeric enclosure, comply with the Polymeric Impact Test in Clause 16.41 of CSA C22.2 No. 250.0, using a preconditioning temperature of 0 ±2.0°C (32 ±3.6°F); and
A circuit operating at Class 2 or LED Class 2 power levels (see Annex A) in which voltage levels are below those that present a risk of electric shock (see Clause 3) is not required to be subjected to Items (a) and (b) above. | |||||||||||||||||||
6.3 | Update Remark: Aligned weatherometer and impact test requirements for polymeric enclosures in wet locations. Clarification of Class 2 and LED Class 2 exemptions. A unit intended for use in wet locations shall (a) be subjected to the environmental tests specified in Clause 9.12 unless all live parts and traces on the printed wiring board are potted (see Clause 7.7) or conformal coated (see Clause 8.7.2); (b) if provided with a polymeric enclosure, comply with the weatherometer test specified in of CAN/CSA-C22.2 No. 0.17 and with the Polymeric Impact Test in Clause 16.41 of CSA C22.2 No. 250.0, using a preconditioning temperature of minus 35.0 ±2.0°C (minus 31.0 ±3.6°F), and
A circuit operating at Class 2 or LED Class 2 power levels (see Annex A) in which voltage levels are below those that present a risk of electric shock (see definition in Clause 3) is not required to be subjected to Items (a) and (b) above. | |||||||||||||||||||
8.3.4 | Update Remark: Updated requirements for soldered connections Version 2012 (Old): Soldered connections shall be mechanically secured before soldering or comply with at least one of the following acceptable methods:
Note: A soldered connection supplied by a Class 2 or LVLE source does not require additional mechanical securement if detachment will not reduce spacings to non-Class 2 or non-LVLE circuits below the applicable required spacings specified in Clause 8.8. Version 2014 (New): Soldered connections to printed wiring boards shall be secured by one of the following methods:
| |||||||||||||||||||
8.4 | Info | Supply and load connections | ||||||||||||||||||
8.4.2.1.5.2 | Conduit closure plugs shall be suitable for the purpose with respect to environmental and enclosure flammability criteria. | |||||||||||||||||||
8.4.2.1.5.3 | Conduit and other knockouts or twistouts shall be secured in place so they can be removed without distorting the enclosure but remain in place during normal handling, as determined by the Knockout Secureness Test, Clause 9.14. | |||||||||||||||||||
8.6.3 | New clause: The insulating materials within an LED package, where the relative thermal index (RTI) or the generic thermal index is exceeded, shall be evaluated in accordance with Clause 9.15. | |||||||||||||||||||
8.7 | Info | Printed wiring boards Update Remark: Updated requirements | ||||||||||||||||||
8.7.1 | Printed wiring boards shall comply with the requirements of Annex C. | |||||||||||||||||||
8.7.2 | Conductive traces shall be bonded to the substrate for the minimum conductor width and maximum unpierced area as required by the adhesion requirements of Annex C. Notes:
| |||||||||||||||||||
8.7.3 | Temperatures measured in the temperature test of Clause 9.3 shall be in compliance with Table 8. Note: A printed wiring board connected within a Class 2 or LED Class 2 circuit need not comply when means (suchas position, distance, or barrier) are provided to ensure that the limited energy traces cannot contact non-energy limited live parts should the traces become detached from the substrate. | |||||||||||||||||||
8.7.4 | The flammability rating of the printed circuit board shall be in accordance with the requirements of Clause C.2.2 and Clause C.2.3 of Annex C. Note: A circuit supplied by a Class 2 power source or LED Class 2 Controlgear need not comply. | |||||||||||||||||||
8.7.5 | Printed wiring boards for direct support of current carrying parts shall comply with the requirements of Clause 5.7.1.3 and Clause 5.7.1.4 of CSA C22.2 No. 250.0. Notes:
| |||||||||||||||||||
Table 8 |
* There are no temperatures specified; the manufacturer's rated temperature of the material or component shall be used. † Unless the material is thermal-setting, the maximum potting-compound temperature, when corrected to a 40 °C ambient temperature, is 15 °C less than the softening point of the compound as determined by ASTM E28. | |||||||||||||||||||
9.3 | Info | Temperature test | ||||||||||||||||||
9.3.17 | Note: Additions to existing requirements are underlined The junction of the thermocouple shall be firmly secured with the point on the surface on which the temperature is to be measured. When radiation might affect thermocouple measurement of polymeric material, the junction of the thermocouple may be embedded within the material such that the thermocouple junction is shielded from direct optical radiation. The thermocouple shall consist of wires not larger than 24 AWG (0.21 mm2) and not smaller than 30 AWG (0.05 mm2). Thermocouples consisting of 30 AWG (0.05 mm2) iron and constantan (Type J) wires shall be used whenever a referee temperature measurement by thermocouples is necessary. Thermocouples consisting of chromel-alumel (Type K) or copper-constantan (Type T) wires may be used if it is determined that high-frequency operation results in eddy current heating of iron and constantan thermocouples. | |||||||||||||||||||
9.5 | Info | Abnormal tests | ||||||||||||||||||
9.5.12 | Note: Additions to existing requirements are underlined During each test, the grounding means, if provided, shall be connected to ground through a 3A non-time delay fuse, and the unit shall be draped on a softwood surface covered with white tissue paper and draped with a double layer of cheesecloth conforming to the outline of the unit. The white tissue paper shall be nominally 0.001 in (0.025 mm) thick, commonly used for gift wrapping. The cheesecloth shall be untreated cotton cloth running approximately 34 g/m2 (0.11 oz/ft2), with a thread count in the range of 10 – 13x9–12 threads/cm (25 – 33 x 22 – 30 threads/in). The unit shall be energized at rated input voltage and frequency. The supply circuit shall be connected in series with a 20 A branch circuit-rated fuse (time delay type), of which the characteristics are such that the fuse does not open in less than 12s when carrying 40 A. | |||||||||||||||||||
9.7 | Info | Leakage current measurement test | ||||||||||||||||||
9.7.1 | Update Remark: Updated test procedure A cord-connected unit rated for a nominal 250 V or less supply shall be tested in accordance with this Clause. Leakage current shall not be more than
Version 2014 (New): A unit connected to a branch circuit supply voltage shall be tested in accordance with Clause 9.7. Leakage current shall not be more than
Note: This test can be waived for a remotely-mounted unit connected and grounded via a fixed supply connection or if the unit is an integral part of an end-product luminaire with a fixed supply connection and the end-product standard for the luminaire does not require a leakage current measurement when the supply connection is fixed. | |||||||||||||||||||
9.7.7 | New clause: Using a commercially available meter having the network shown in Figure 5 or built to conform to the ANSI/UL C101 meets the intent of these requirements. The meter shall be set to “reaction” curve. | |||||||||||||||||||
9.14 | Info | New test clause: knockout secureness test | ||||||||||||||||||
9.14.1 | A force of 44 N (10 lbf) shall be applied to a knockout for 1 min by means of a 6.4 mm (0.25 in) diameter mandrel with a flat end. The force shall be applied to the exterior surface of the knockout, in a direction perpendicular to the plane of the knockout, and at the point most likely to result in movement. | |||||||||||||||||||
9.14.2 | The knockout shall remain in place, and the clearance between the knockout and the opening shall be no more than 1.6 mm (0.063 in) when measured after the force has been removed. | |||||||||||||||||||
9.15 | Info | New test clause: Thermal aging test | ||||||||||||||||||
9.15.1 | LED packages with insulating materials, as described in Clause 8.6.2(e), shall be aged in a full-draft oven at a temperature and time chosen from the graph in Figure 8 using the index line that corresponds to the maximum junction temperature as specified by the manufacturer. All samples shall be conditioned for 1000 hours unless otherwise agreed by all concerned. LED packages shall not be subjected to conditioning less than 300 hours. Three representative samples are tested. After this oven conditioning, all three samples shall withstand the Dielectric Voltage tests described in Clause 9.4. | |||||||||||||||||||
9.15.2 | The air oven shall be essentially as indicated in ASTM D5423 (Type II ovens) and ASTM D5374. A portion of the air may be recirculated, but a substantial amount of air shall be admitted continuously to maintain an essentially normal air content surrounding the representative LED package. The oven shall be adjusted to achieve 100 – 150 complete fresh-air changes per hour. |
CUSTOMERS PLEASE NOTE: This Table and column "Verdict" can be used in determining how your current or future production is or will be in compliance with new/revised requirements.
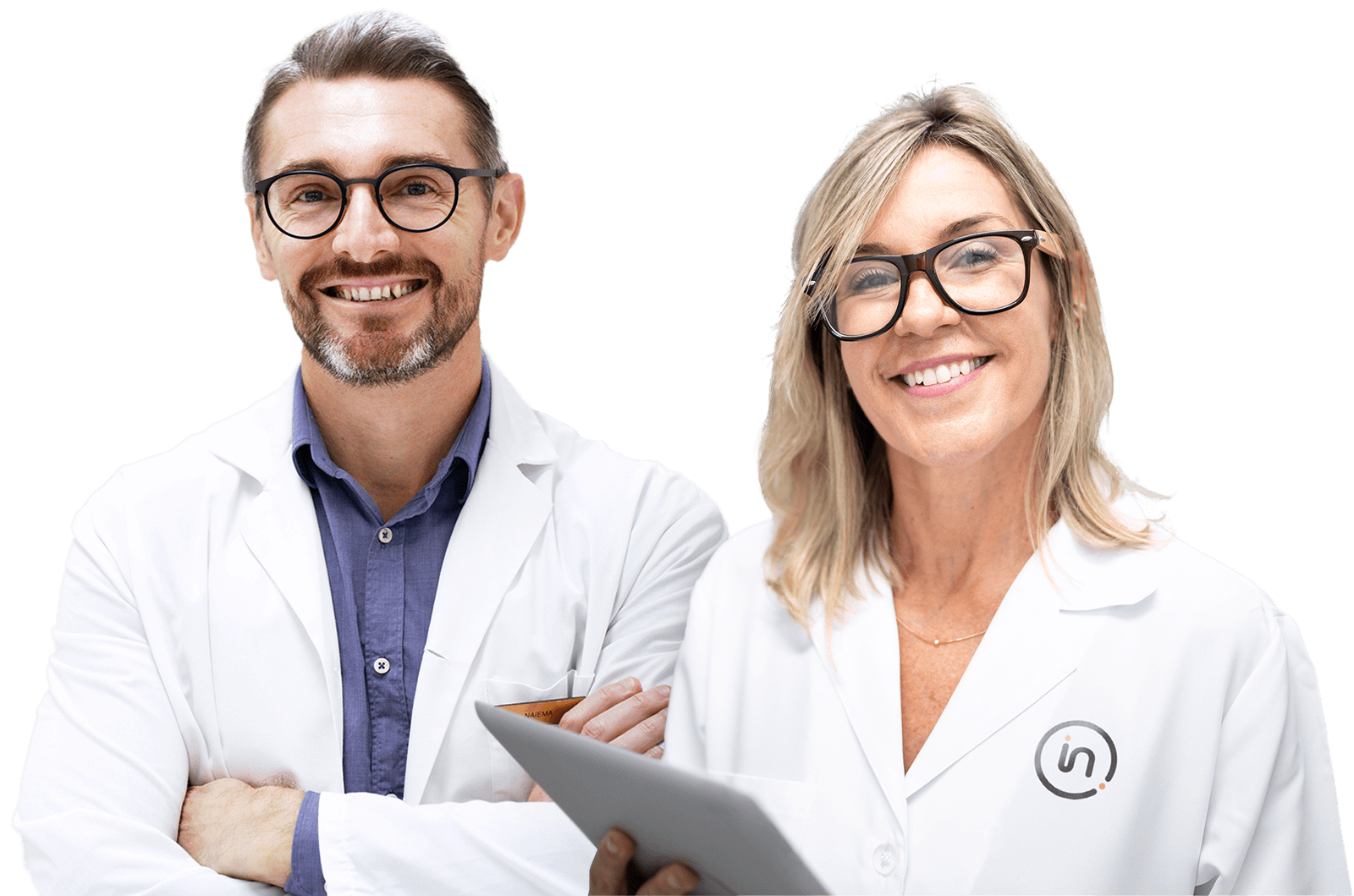