Save time and money in product development using HALT and HASS testing.
Highly Accelerated Life Test (HALT) and Highly Accelerated Stress Screen (HASS) are often used in conjunction with one another. During the HALT process, a product is subject to increasing stress levels of temperature and vibration (independently and in combination), rapid thermal transitions, and other stresses specifically related to the operation of your product. The information goals of HALT are to:
- Determine multiple failure modes and root causes
- Determine functional operating limits
- Determine functional destruct limits
- Focus on thermal and vibration stresses (first separately, then combined)
HALT was developed specifically for solid state electronics, but can be applied to any product, with the correct equipment. In general, the information goal of HALT is most effectively met by testing at the lowest possible sub-assembly:
- Consider a balance between a "functional assembly" and determining the technological limit of a product feature
- Consider removing structure that dampens vibration or blocks air flow; reducing the applied stresses to sub-assemblies
- Consider that loss of critical circuitry or connections may affect the sub-assembly tested
Highly Accelerated Stress Screen- HASS
Once the HALT process has been completed, and the product has been ruggedized, we can develop a custom production screen to identify process defects. Running a HASS:
- Apply all stresses simultaneously. During vibration, continuously ramp temperature between brief dwells at extremes.
- HASS stress levels are based on HALT limits.
- Include any "critical" additional product stresses (as determined from HALT, e.g. product power).
- Conduct precipitation screen and evaluate product beyond operating limits, near destruct limits.
- Precipitate failures in product due to "latent" defects.
- Conduct detection screen and evaluate product near operating limits. Confirm and explore precipitation screen failures, and other hard and soft failures.
By using a properly designed accelerated test to failure you can find the non-intuitive failures that would normally require months or even years in the field to identify. Finding real failure modes earlier in the development process can save time and potentially even avoid significant warranty issues.
Related Links
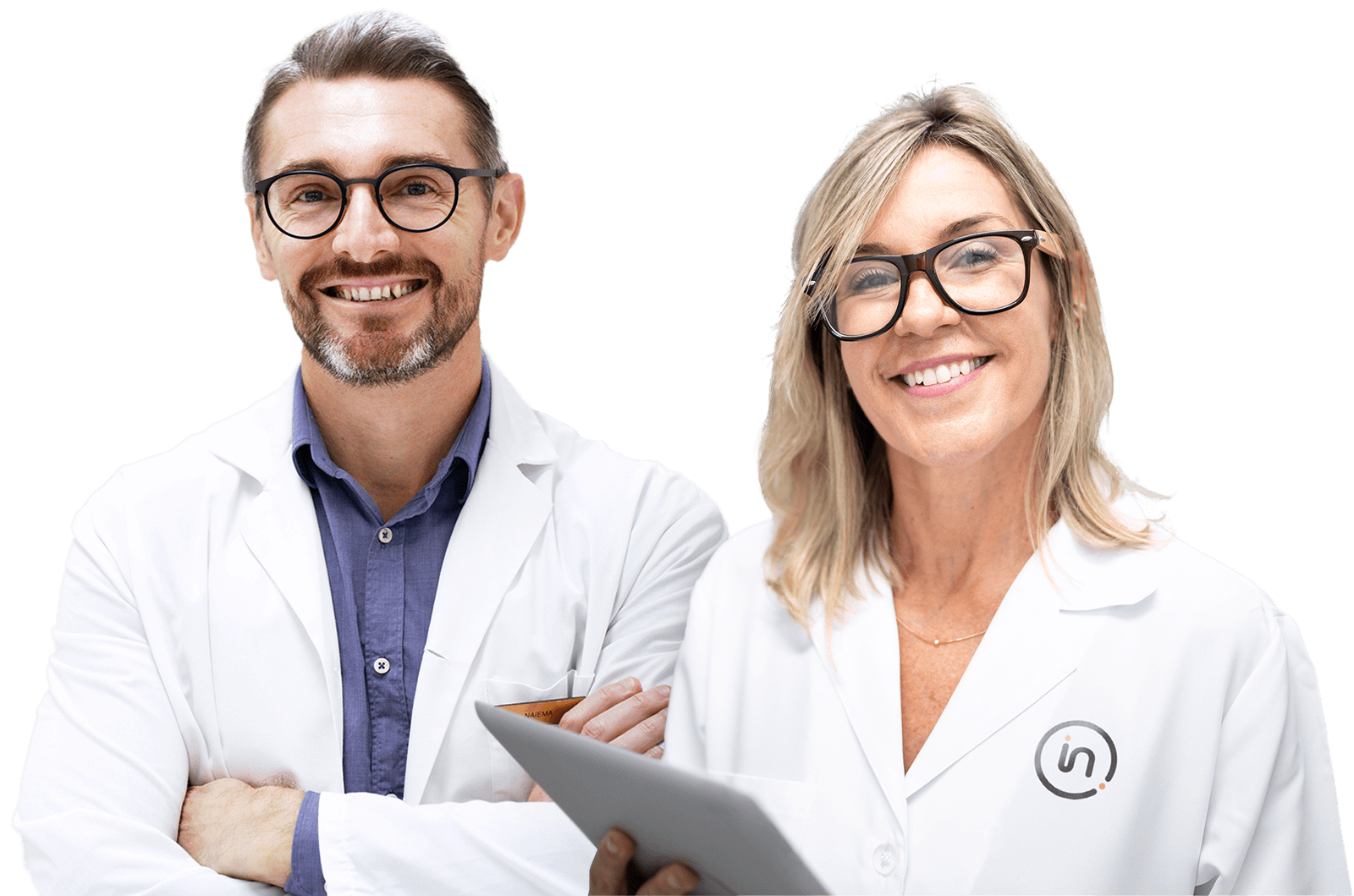