Through Accelerated Reliability Testing Intertek will work with you to uncover design defects or weaknesses that may not have been realized during product design
Accelerated reliability uses a simple premise and some complex math to achieve a reliability estimate of a product for particular conditions. As a particular source of stress is increased, time to failure exponentially decreases. This effect is used to design the accelerated reliability test.
A simple example of this effect is the fatigue curves of steel. As the stress level rises, the time to failure drops exponentially. Also the logarithmic rate of change is affected by the change in the physics of accelerated reliability.
In an accelerated reliability test, several sets of parts are tested at stress levels much higher than the expected service level. For example, 8 parts might be tested simultaneously (Test One) until four parts failed. This would establish one point on the accelerated reliability graph. Then another 8 parts would be tested at a slightly different stress level until four parts failed (Test Two). Testing of groups of parts at different stress levels would continue until enough data was collected to extrapolate the service condition time to failure.
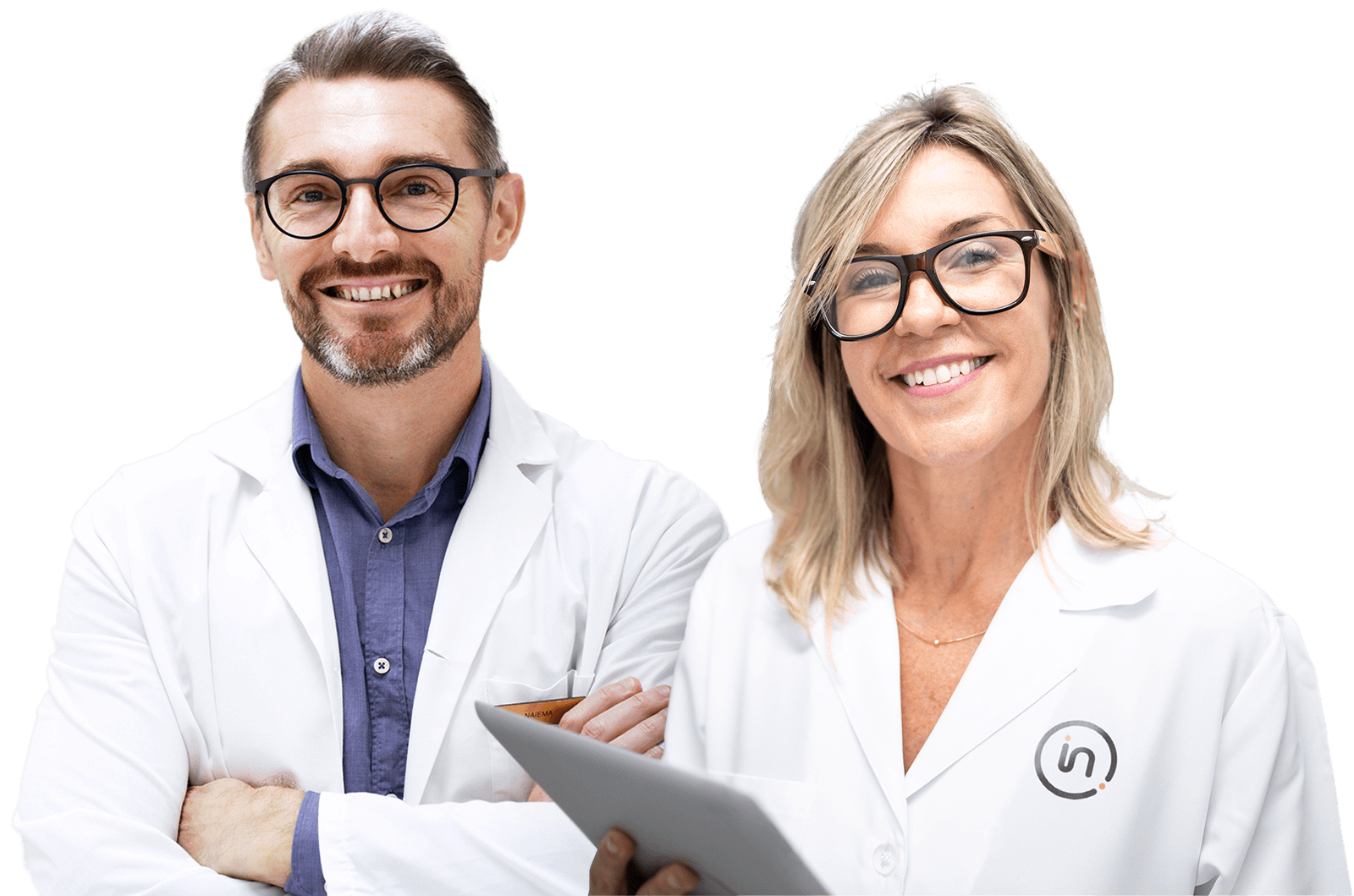