Aware RealTime is an Asset Performance Management (APM) software designed to be easily added to the current generation of power plant data acquisition and control systems (DCS).
Aware RealTime (Aware RT), formerly COSTCOM, computes equipment damage accumulation rates and dollar costs for baseload and cycling operation. This is done by drawing real-time measurements from the DCS system and computing stresses and damage accumulation. This approach draws on Intertek’s cost of cycling analysis that derives dollar costs for defined load transients.
Power plants that often start, stop, cycle, two shift, and operate above a unit's rating impact the life of the unit and total associated unit operating costs.
Intertek has developed a real-time operations product called Aware RT that is specifically calibrated to display the maintenance, capital replacement, and wear-and-tear costs associated with these potentially damaging operations.
Intertek’s APM solution allows asset owners to improve asset integrity, by optimizing operating costs, minimizing risk and improving asset reliability. Aware RT determines the cost impacts of increasing ramp rates, MW load transient ranges, and shortened startup times. By using Aware RT, operators can learn how to control cycling operations to reduce costs.
A large coal fired power plant in North America has utilized Aware RT to determine real-time operations and maintenance (O&M) costs from cycling. You can download the case study here.
Intertek has analyzed cycling and operating costs for over 500 power generating plants using our Total Quality Assurance approach. Aware RT has been developed to update energy bids in the market to recover cycling costs, monitor and utilize cycling costs, provide predictive maintenance insights, optimize cycling operations and costs, monitor damage accumulation rates, improve control of load transients, train operators on cycling operations, and manage equipment life.
Aware RT’s algorithm follows these steps to measure and monitor damage on plant components:
- Machine Learning
- Anomaly detection
- Statistical Analytics
- Layer statistical analysis with Engineering and Materials First Principles
- Compute Fatigue and Steady State damage
- Visualization
Aware RT tracks all major equipment at a plant including, the boiler/HRSG, gas and steam turbine, piping system, fuel handling system, and other balance of plant equipment. Aware RT also monitors powerplant water chemistry, fuel burn and heat rates, as well as emissions control systems to quickly identify damaging transients.
The key features of Aware RT are:
- Simple, user friendly interface which works with the plant’s real time data acquisitions system.
- Configurable “Damage Score” for each cycling trend.
- Allows operators to visualize degree of operational flexibility and impact on unit damage.
- Identifies and documents Ramp rates and startup and shutdown transients clearly with a summary report of each event
- Plant Managers can review and compare historical trends to gauge operator procedures. Management can determine countermeasures to improve startup and shutdown and transient load swings
- Helps train operators. By using Aware RT, operators can learn how to control cycling operations in order to reduce O&M costs, improve reliability and extend operating life.
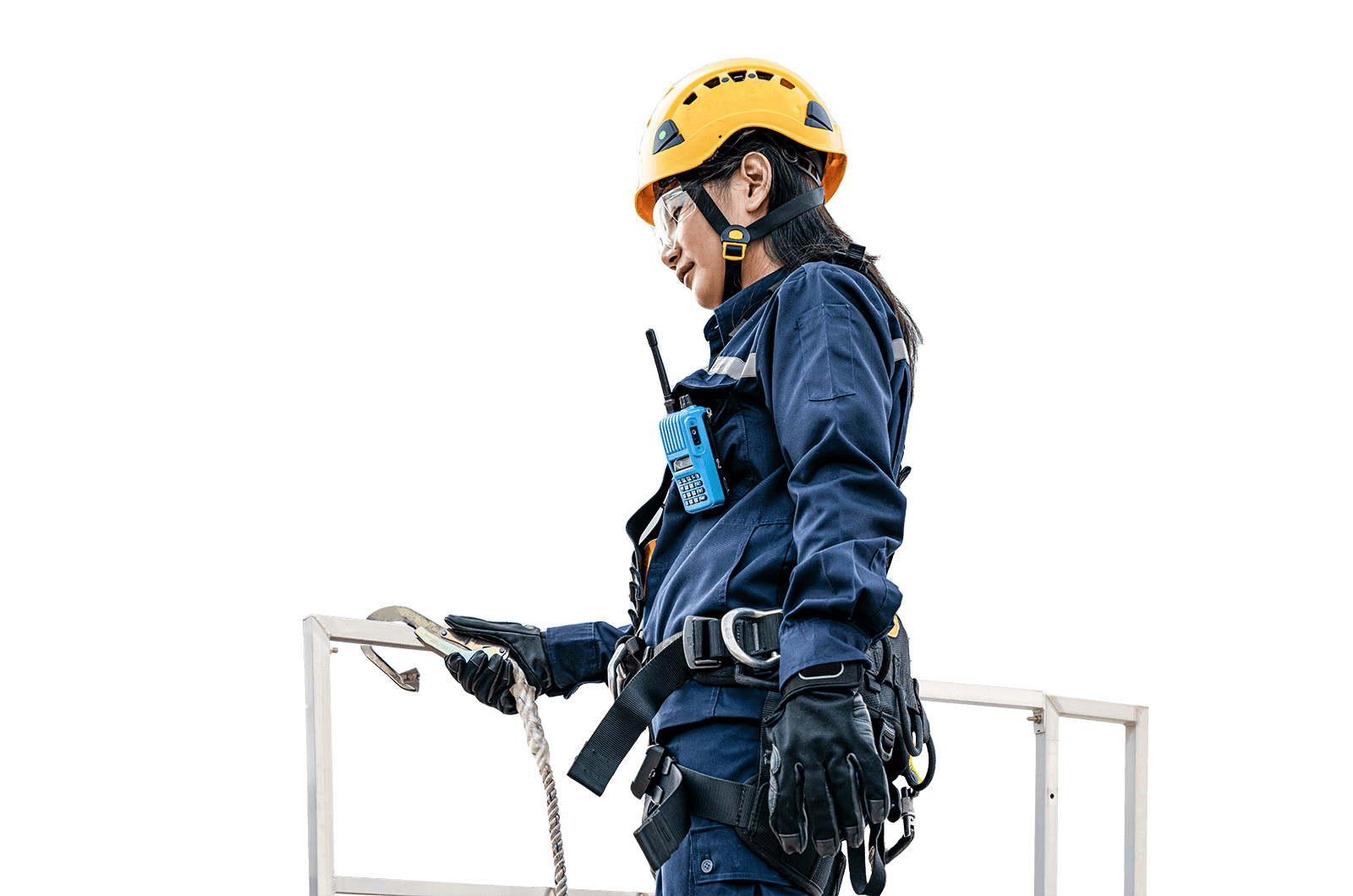