Avoid forced outages and improve your planned outage work. Map tube failures, repairs, thickness and oxide scale data; manage visual inspections and automate the flow of information/work with our boiler integrity management software.
The Aware Boiler Integrity Module is in use at over half the boilers in North America to improve reliability, availability and safety.
Faster Recovery With Our Boiler Integrity Aware Module
When a tube failure occurs, personnel must quickly identify the material and/or stock number as well as the weld procedure to be used. With the Aware boiler integrity software, this information is available via any computer with just a few mouse clicks. Simultaneously, personnel can see the previous inspection findings, UT readings, and other tube failures for the relevant component or a similar component/boiler in the fleet. This information provides critical input for determining what type of repair should be carried out so to avoid another forced outage.
While reviewing the information, personnel can document the current tube failure and enter whatever information is known at the time. When the unit returns to normal operation, the rest of the information can be entered, and if an R-1 form is required, can be printed directly from the system. Having quick and easy access to the right data at the right time allows plant personnel to perform their job functions more efficiently and return the unit to full operation in shorter time. The Aware boiler software improves the bottom line by enabling a faster recovery, and therefore reducing the duration of forced outages.
Boiler Integrity Management Software Helps You Avoid Forced Outages
A key indicator of where and when future leaks are going to occur is by way of the past history of tube leaks at an individual unit or across a fleet of similar units. The Aware boiler integrity software provides the tools necessary to record, view, and report tube failures by displaying them on plant-specific interactive CAD drawings providing Total Quality Assurance. Tube failures that have occurred during a specified date range are displayed on a drawing with filters that identify such information as failure cause, description, repair type, repair status, and unit. This visual analysis tool, along with the powerful reporting and trending functions, allows engineers to have improved insight into the boiler’s condition and how quickly the equipment is aging.
UT readings and wastage rates are key indicators of future problems, therefore the Aware boiler integrity software has been designed to manage this data as well. Users can take readings, upload them into the system and calculate a wastage rate over a specified window in time. Both measurements and wastage rates can be displayed on the drawings, and color-coded symbols are automatically applied to highlight potential trouble spots.
By reviewing past failures, inspections, and UT measurements, analysts can better predict what trouble spots are likely to lead to forced outages.
Manage Boiler Inspection Workflow With Our Software
Aware can be used to manage your boiler inspection program and the flow of information and resulting work. The software guides an inspector by presenting forms to be filled in that are specific to each component (e.g. waterwall, superheater. Etc), and each activity (e.g. visual inspection, UT Data, etc.). The inspector has specific fields to fill in to document each activity, such as "Conditions Found", "Recommendations", "Priority", etc, which enforces a standardized approach to reporting inspection findings. Standardization insures that the right information is collected for each activity, and facilitates reviews of the findings.
By adding the optional Mobile Aware capability, an inspector can use handheld computers to document inspections while inside the boiler – dramatically reducing the time required for report writing.
During the outage, daily work list reports are generated providing a detailed list of recommendations made that day and details of the conditions found that give craft personnel a better understanding of the work required. At the end of the outage, a consolidated report is automatically generated including photographs, conditions, recommendations, and tables.
If desired, integration with a Computerized Maintenance Management System (CMMS) can be implemented to create and/or amend work orders for the work to be done.
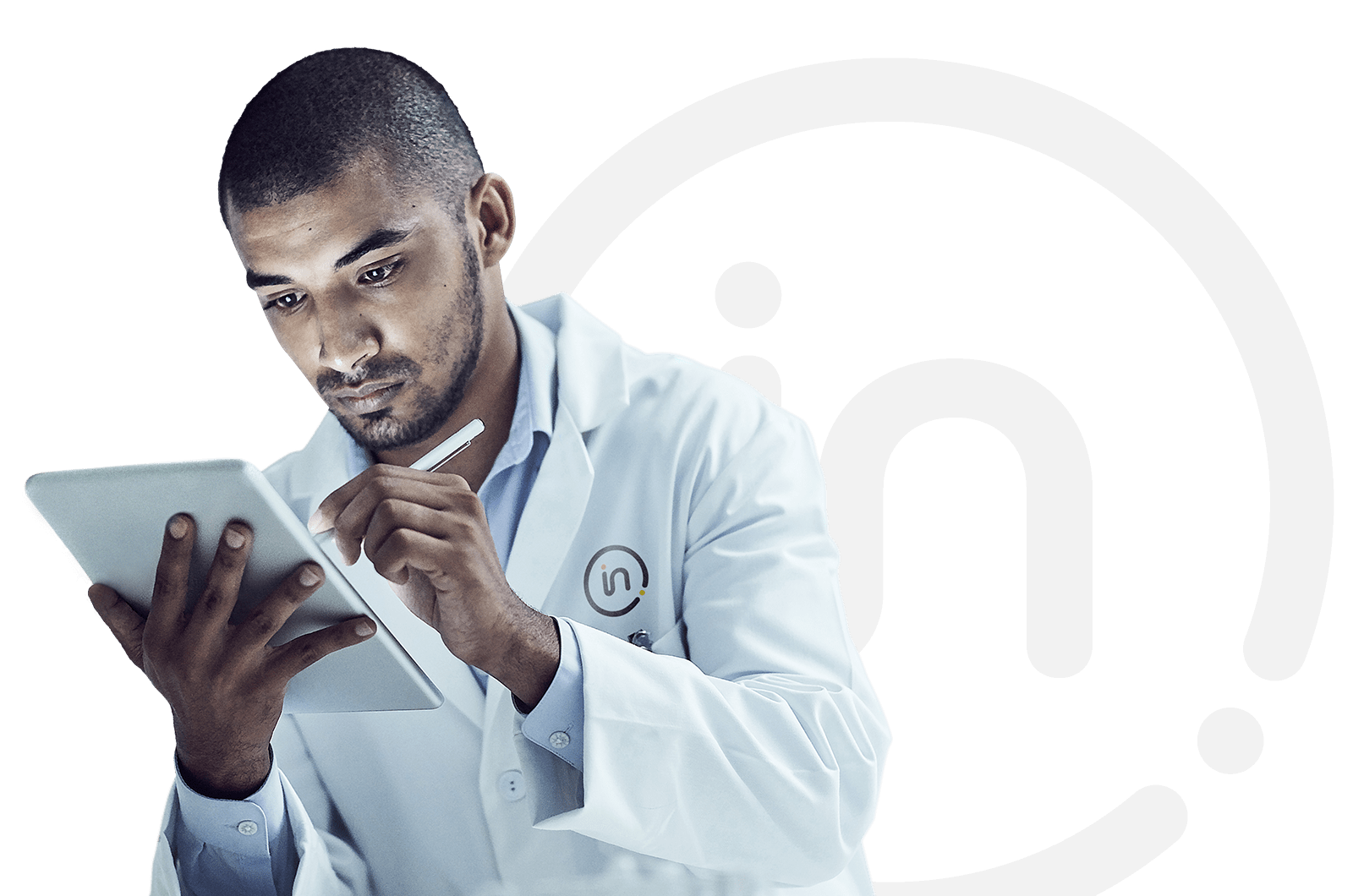