ASTM C1521-13: Evaluating Adhesion of Installed Weatherproofing Sealant Joints
Standard: ASTM C1521-13 – Standard Practice for Evaluating Adhesion of Installed Weatherproofing Sealant Joints
Scope: This practice describes destructive and nondestructive procedures for evaluating adhesion of installed weatherproofing sealant joints. The destructive procedure stresses the sealant in a way as to cause either cohesive or adhesive failure of the sealant or cohesive failure of the substrate where deficient substrate conditions exist. The nondestructive procedure places strain on the sealant and a stress on the adhesive bond. The nondestructive procedure can be used for continuous inspection of 100% of the joints or for any areas where deficient conditions, which are inconsistent with the practices of ASTM C1193, are suspected. The Flap Procedure is utilized to evaluate the bond at each substrate, particularly if the substrates on each side of the joint vary.
Applicable Products: Weatherproofing sealant joints.
Test Procedure:
Non-destructive Procedure – A probing tool is utilized that is at least 1/8” narrower than the width of the sealant joint to be evaluated.
Technique #1: Using the probing tool, the center of the sealant bead is depressed to create an elongation strain on the sealant joint. The depth of the depression is recorded as a percentage of the width of the bead.
Technique #2: Locating the probing tool adjacent to the sealant/substrate bond line, the sealant bead is depressed to the extent that it appears the sealant is about to fail cohesively. The sealant bead should be depressed in such a way that the probing tool does not contact of scrape against the substrate, nor slide toward the center of the joint.
Destructive Procedure – The “Tail” Procedure consists of cutting through the sealant 6-inches along the bond line at both surfaces. The sealant bead is cut across horizontally to release one end of the “tail” that is formed.
Method A: Mark the cut portion of the sealant 1 inch from the adhesive bond. Grasp the sealant “tail” at the mark 1 in from the adhesive bond. Pull the tail at an angle of 90 degrees to the substrate to effectively elongate the 1 inch mark to two times the stated movement capability of the sealant. Record the type of failure that occurs and the distance of the mark from the adhesive bond when failure occurred, or the distance recommended by the manufacturer without causing failure.
Method B: Mark the cut portion of the sealant 1 inch from the adhesive bond. Grasp the sealant tail at the mark 1 inch from the adhesive bond. Various tests can be performed pulling the tail slowly at an angle of 30, 90 or 150 degrees to the substrate, keeping the tail in line with the sealant bead as precisely as possible. Monitor the extension to determine the elongation resulting in failure. If sealant begins to experience cohesive failure, stop pulling and readjust the grasp on the tail and begin pulling again. The tail is pulled in whatever direction or manner that best avoids cohesive tearing and encourages adhesive failure to occur. Repeat the procedure as necessary to evaluate adhesion to both substrates forming the joint.
Flap Procedure – Sealant is cut 3 inches along the bond-line on the substrate opposite to the substrate to be evaluated. Make two cuts across the sealant bead horizontally at each end of the 3 inch cut. Pry up the flap that is formed by the three cuts through the sealant bead. Grasp the flap near the edge opposite the bond line to be evaluated. Pull the flap in the tensile mode until the onset of adhesive or cohesive failure occurs. Stop pulling and grasp the flap near the other end. Pull the flap in a shear mode until the onset of adhesive or cohesive failure. Trim away the portions of the flap that have failed. Bend, twist and/or rotate the flap until adhesive or cohesive failure occurs.
End Result: The objective of the Destructive Procedure is to characterize the adhesive/cohesive performance of the sealant on the specific substrate by applying whatever strain is necessary to effect failure of the sealant bead. The Nondestructive Procedure may result in the failure of a deficient substrate before effecting a failure in the sealant. The weatherproofing may require additional remediation in order meet the performance criteria.
You may be interested in...
Knowledge Center
Building Health & Wellness: An Overview of Services
Acoustical Testing & Consulting Resources
Remote Pre Inspections for NFPA 80 / 101
Protek - Safety. Everywhere. Every Day
Fire Doors 101: Your Guide to Testing and Certification - Webinar Recording
Tornado Testing & Certification Requirements - Webinar Recording
Plumbing Products Testing & Certification - Webinar Recording
The Evolving Code Evaluation Process White Paper
Proposition 65 & the Furniture Industry Webinar Recording
Why Planning for FCC Certification is Key to Success in the Door Hardware Industry White Paper
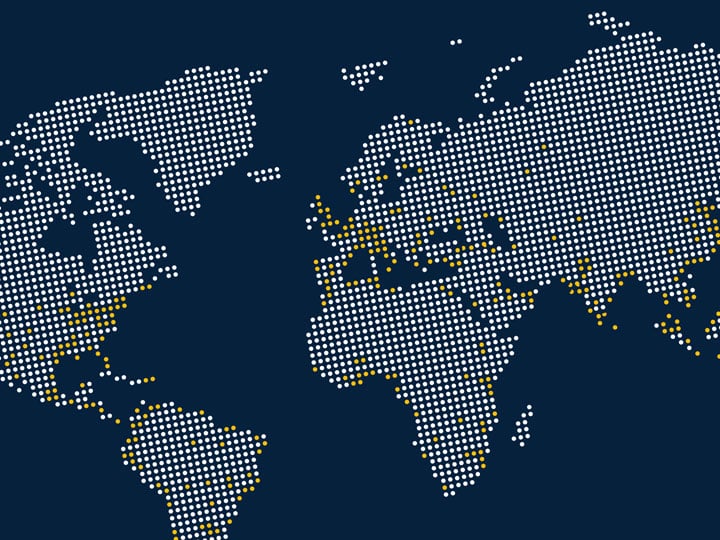
Upcoming Tradeshows & Events
Resources
- Search and Buy Building & Construction Standards
- SpecDirect
- Building Products Directory
- Project Connect (formerly myATI) – B&C Products
- Construction Hive – B&C Projects (PSIQest)
- My TestCentral
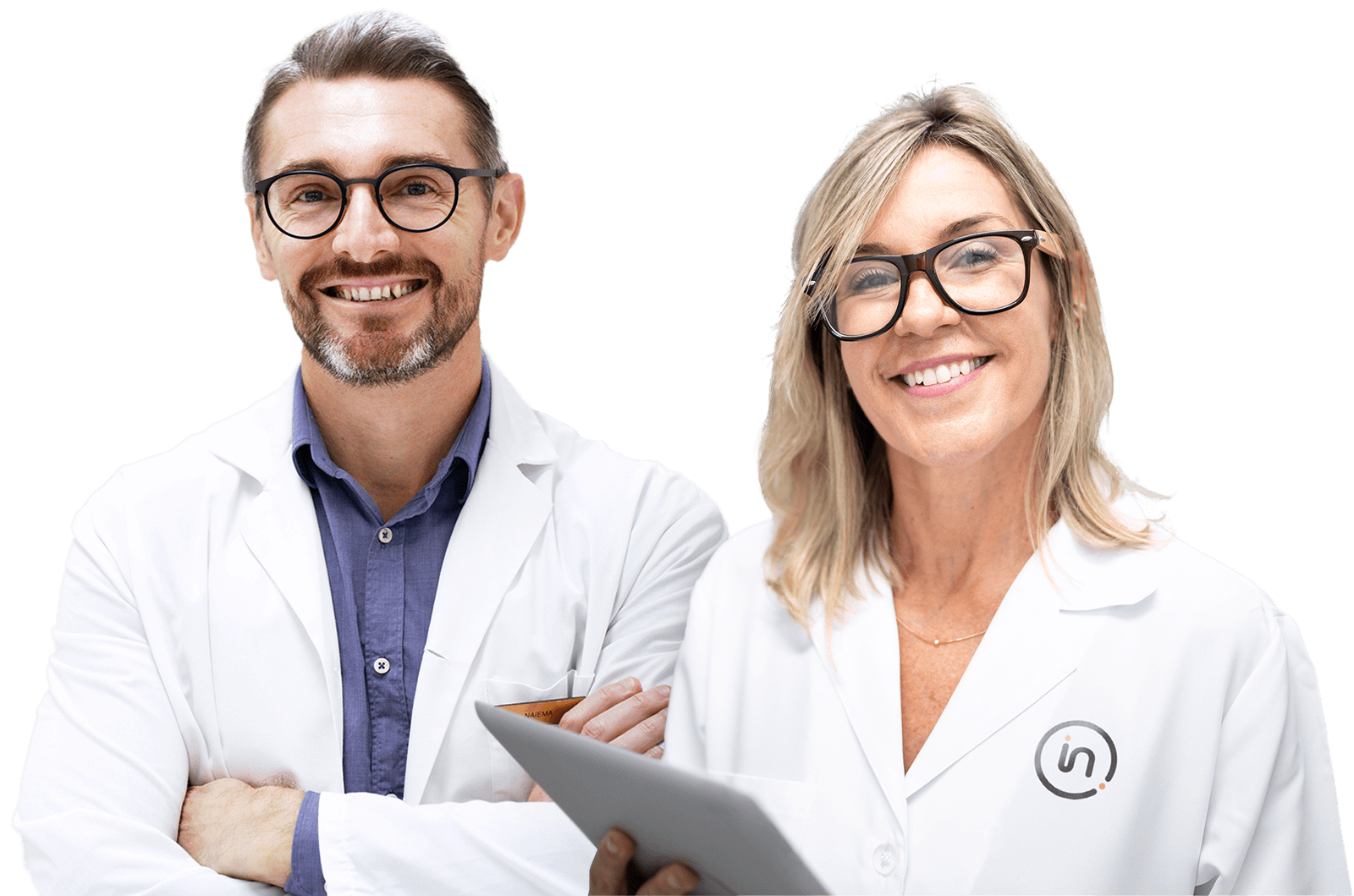