Trends in Sustainable Building Materials - Part 2
20 Jun 2023
A look at the tools used to evaluate the environmental impact of building products and processes
In part one of this blog, my colleague Alan Scott looked at some of the trends that are driving attention toward reducing embodied carbon in the design and construction of buildings and infrastructure. In part two, I’m going to focus on the tools we use to evaluate the sustainability of products and processes, including life cycle assessments and environmental product declarations.
What is a Life Cycle Assessment?
A life cycle assessment (LCA) is a process or tool used to evaluate the environmental burdens associated with a product, process, or activity over its entire life cycle (from resources to end-of-life). LCAs are used to determine the environmental impact a product or process may have on the world.
How does an LCA work? An LCA uses the individual environmental impact data for a process or material. An LCA is not just about carbon footprint, it looks at various environmental impact indicators to account for other factors such as climate change, ozone depletion, acidification, eutrophication in freshwater, photochemical ozone formation, human toxicity, eco-toxicity, and water use, to name a few.
The data is collected and modeled from around the world for different materials and different industries, because the carbon footprint and all these other environmental metrics are different by industry and location. For example, if you are using steel mined in Australia and refined in China, it’s going to have a different environmental impact than steel mined in Australia and refined in the U.S., so every detail is critically important to getting the environmental impact correct.
The data is compiled into databases, which are constantly kept up to date. So, even if nothing else has changed about your product, it is possible that the results of an LCA or environmental impact study change over time. This is why LCAs have time limitations to them.
An LCA takes data at an individual material or process level and then applies it. In order to apply it, we look at the different life cycle stages of a construction project, to consider the individual impact in each step of the life cycle. This is very complicated for just one product or material, imagine how complicated it is to do for a whole building, where you have to look at the entire supply chain for thousands of components used. Because of this, we are starting to see a proliferation of environmental product declarations (EPD) used in industries with complex products that use a lot of components.
What is an Environmental Product Declaration?
An EPD is a verified environmental impact of a product, material, or commodity, and allows the user of a product to trust and understand the environmental impact of including the product or component in their project.
To ensure that everyone is measuring the same way, there are product category rules (PCR) that dictate certain assumptions that can be made and ensure that everyone is following the same rules when conducting their LCA. There are rules on when you can use things like primary and secondary data, what boundaries required for reporting, what assumptions can be made around the lifespan, the use or disposal of certain products or materials. Think of PCR as the rulebook for your product or product categories, they ensure that EPDs can be to compare apples to apples.
EPDs are different than an LCA because they are verified by an independent third party and is registered by a program operator. The process of obtaining and EPD looks like this:
- Identify the correct PCR
- Identify the Program Operator
- Determine optimal approach for LCA
- Data Collection (Primary vs Secondary)
- Modeling
- Checks and Balances
- Develop Report
- Third Party Review
- Submission
- Publication
The timeline for obtaining an EPD is at least eight weeks, but some can take over a year. If you are going to obtain an EPD, take this into consideration and plan your timelines accordingly.
Some common misconceptions include having an EPD doesn’t necessarily mean your product is sustainable or better than products that do not have EPDs. An EPD is really just a certified document according to a set process that determines what the environmental impact of your product is. It’s very much like a certification of a product or component to a standard.
For a more in-depth look at how LCAs and EPDs are used in the building and construction industry, watch our on-demand webinar: Declaring and Use of Sustainable Materials for Eco-friendly Buildings.
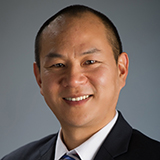
Wesley Chen,
Vice President Sustainability, Quality & Safety, Intertek Assuris
During his 16 years with Intertek, Wesley has supported retailers and brands with quality management solutions. He is currently part of a group of global consultants that supports clients across the value chain to achieve product and organizational goals that are aligned with company values. This includes delivering insights in sustainability, quality, and safety and providing advice on strategies for achieving goals and integrating systems to ensure success.
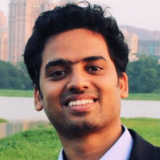
Vijay Thakur,
Sustainability Manager, Intertek Assuris
Vijay leverages his expertise in life cycle assessment (LCA), environment product declaration (EPD), circular economy, design for environment, carbon footprint, and product environmental compliance to support clients in achieving their sustainability goals.