Deconstructing Materials, Parts, and/or Subassemblies
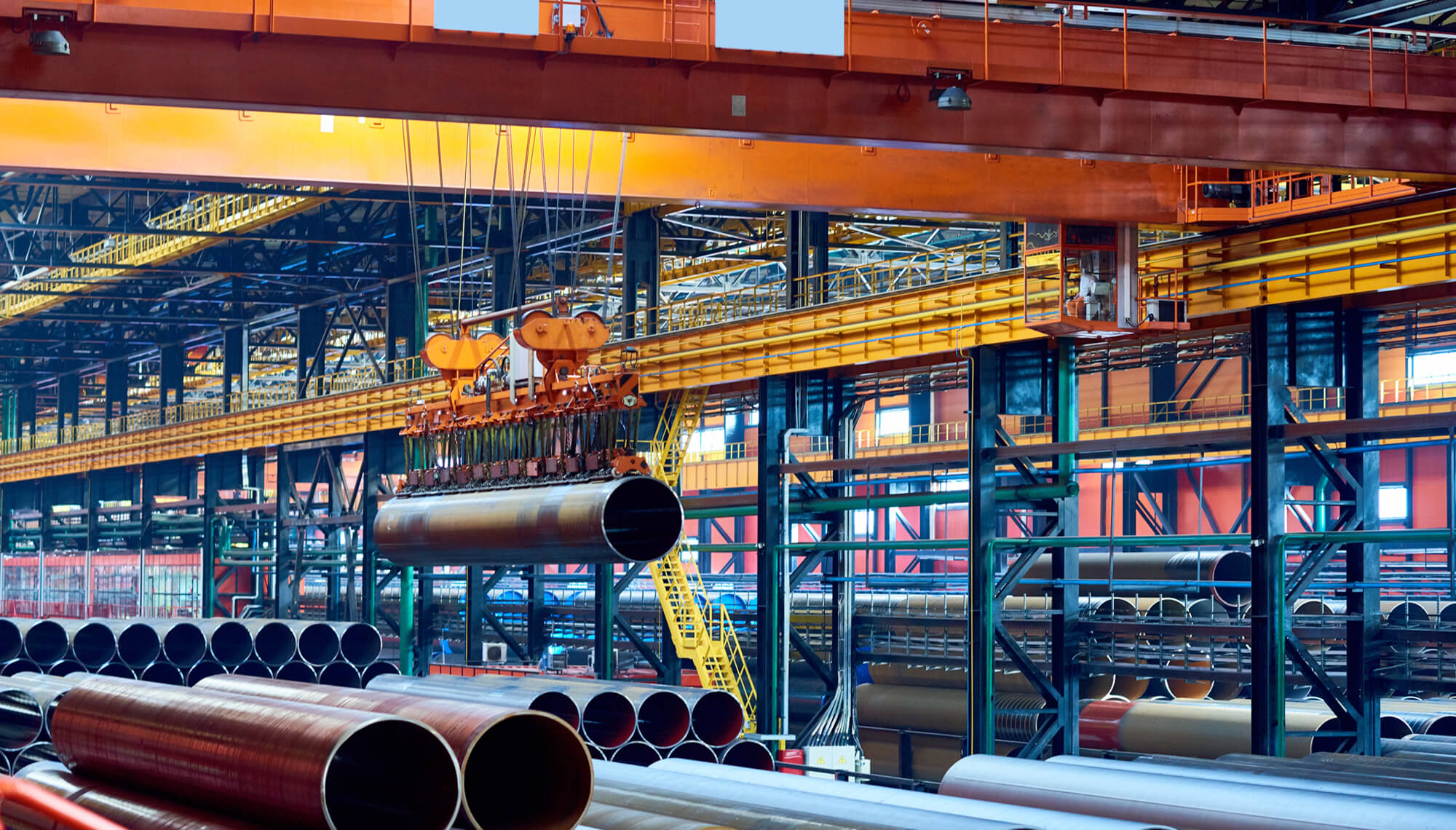
28 May 2019
Challenges in Chemical Regulatory Assessment
The Conformity Assessment Challenge
Since the introduction of IEC 63000 and its predecessor EN 50581, assessing products for conformity to chemical regulations has shifted focus from a poorly-defined "due diligence" exercise into a relatively well-defined engineering exercise.
I have found that in general, parts are well-maintained by equipment manufacturers, subassemblies generally so, but materials are poorly understood. This is a critical shortcoming in many cases and has resulted in delayed market access while product testing and engineering changes take place.
A standards-compliant conformity assessment has specific data collection thresholds which must be met, as well as specific informational requirements with respect to the product under investigation.
IEC 630001 requires analysis of "materials, parts, and/or subassemblies" in the product.
When assessing a product design, I often see some variation (see Table 1):
Table 1: PLM View of Subassembly
Part Number |
Supplier |
Supplier part number |
Material |
Finish |
Conformity status |
Conformity risks |
Conformity Document(s) |
1234A |
MetalCo |
1234A |
Steel |
Zinc, paint |
?!? |
?!? |
None |
For a subassembly that is abstracted in this way, the request for conformity documentation sent to "MetalCo" usually results in a response along the lines of:
"If the print is compliant, then the product is <RoHS, REACH, whatever> compliant"
The outcome is generally poor, and the engineering team is left with the IEC 63000 fallback to "determine what further actions are necessary". This must be done on a case-by case basis, given the lack of structure to the material and finish fields (if they were even recorded in the PLM system in the first place).
The question is then, out of the supply chain and design team, who is at fault?
- Not component engineer's fault – the composition of subassemblies is not in their domain
- Not mechanical designer's fault – mechanical designers are usually quite well-informed about materials and their properties
- Not the quality team's fault – the risks associated with materials are readily available and are documented if the QMS is built properly
- Not (quite) the fabricator's fault, who has been following vague instructions all along
I will offer an unusual suggestion, it is the fault of the team which set up the PLM system.
Fixing a Broken Model
The purpose of the PLM system is to maintain a repository of component and related data. It is the understanding and abstraction of this concept which needs to be explored.
Going back to Table 1, a UML class diagram of the data is presented in Figure 1.
Figure 1: PLM System's Anti-Pattern
This is a mistake - If we were to revisit the definition and ask a mechanical designer to describe his or her domain understanding of a "component", we would be told:
"Component X is made from (some materials)"
And not:
"Component X has a material"
Figure 1 is an incorrect interpretation of the business domain. Materials used in construction are simply not an attribute of a component.
I will refer to the Gang of Four's Composite Pattern2:
Use the Composite Pattern when:
- You want to Represent the whole-part hierarchy
- You want clients to be able to ignore the difference between compositions of objects and individual objects
This design pattern encapsulates hierarchy.
Looking back at the business domain, we find components have:
- supply chain
- specification
- compliance risks
and materials have:
- supply chain
- specification
- compliance risks
Subassemblies contain components, materials, and subassemblies. If we abstract these, we get to the following class diagram (see Figure 2).
Figure 2: Composite Pattern, Suggested Application to Component Engineering
By recognizing that materials are entities, as opposed to attributes, they can be:
- Unconstrained by cardinality
- Assigned their own attributes (such as compliance status, substance risks, and test results)
- Reused and substituted
The revised PLM view as previously shown in Table 1 becomes as follows:
Table 2: Amended PLM view
Part Number |
Supplier |
Supplier part number |
Parent |
Conformity status |
Conformity risks |
Conformity Document(s) |
1234A |
MetalCo |
1234A |
|
Mitigated |
By materials |
None |
1234A_1 |
Generic |
Steel |
1234A |
OK |
Lead |
XRF Test |
1234A_2 |
Generic |
Zinc plate |
1234A |
OK |
Chromium |
Wet Cr Test |
1234A_3 |
PaintCo |
Blue #5342 |
1234A |
OK |
DEHP |
Declaration |
Addressing the Challenge
I suspect that the mishandling of the component-material structure comes from producers' incomplete control over their supply chains. Not everything is centrally controlled. Steel can be sourced from anywhere according to metallurgical specification, polymer resins can be sourced from arbitrary chemical companies, not to mention whatever additives are used to provide UV resistance, color, flame-retardance, etc.
This can be solved by noting that a component or material is sourced generically, by some designation in the "supplier" field, as opposed to leaving it out.
The AggregateRisk() and MitigateRisk() operations can take generic sources into consideration. For example, chemical risks can be aggregated from all child components, but mitigating factors can be applied at the lowest (furthest from root) possible level. This will have the result of identifying exactly which design choices the fabricator is responsible for:
- The fabricator is no longer able to state "if the print is compliant…"; the design choices he or she is responsible for are documented in detail
- Items from an uncooperative fabricator can be easily tested, since chemical risks are unambiguously known
- Drill-down into the supply chain is possible if suppliers are known - polymer supplier X is now apparent, and can be addressed directly by a conformity assessment
Note that I have written these operations as software operations, but equivalently they could be implemented as business processes. It is the proper definition of data structure and rigorous application of reproducible processes that is most important.
Intertek Can Help!
Intertek can help manufacturers and the supply chain deal with the challenges these regulatory requirements pose. Need to more information? Visit: /green/restricted-substances-consulting/
References:
1 International Electrotechnical Commission. Technical documentation for the assessment of electrical and electronic products with respect to the restriction of hazardous substances. IEC 63000: 1ED 2016
2 Gamma, E.; Helm, R.; Johnson, R. & Vlissides, J. M. (1994), Design Patterns: Elements of Reusable Object-Oriented Software, Addison-Wesley Professional.
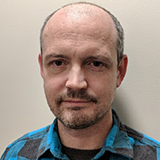
Ian Smith
Regulatory Associate - Engineering, Global Restricted Substances
Health, Environmental & Regulatory Services (HERS)
Ian Smith has been producing Material Science and Data Science solutions to Regulatory problems for over ten years. His customers manufacture products ranging from IT Equipment and Medical Devices to Toys and Sporting Goods, and can be affected by California Proposition 65, EU REACH, global RoHS regulations, persistent organic pollutants, or customer-driven substance restrictions. His evidence-based approach allows manufacturers to prioritize risks based on objective, real-world data, and to direct engineering and test resources in an efficient and cost-effective manner.