Boom, Bang, Slash
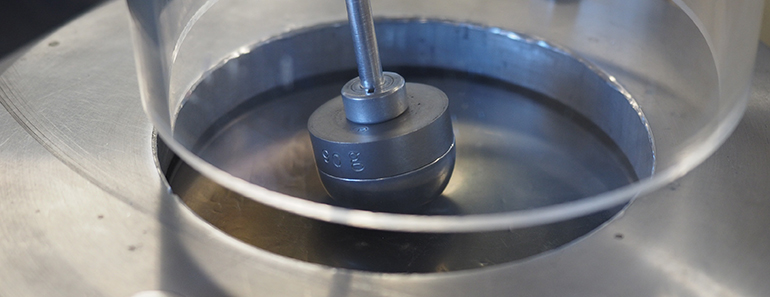
09 Aug 2016
Cutting to the Chase, Testing End-use Performance of Flexible Films
From shipping to storage to end-use, flexible films across multiple industries such as in medical, packaging, building and consumer products will see their share of abuse throughout the product lifestyle as they are bounced, pounced, slashed and mishandled. Therefore, one characteristic key for consideration with flexible film material selection is impact.
There are a number of standardized laboratory test methods to simulate impact in application. Three common tests performed on polymer films and flexible materials to simulate impact include:
- Multiaxial Impact: This sophisticated impact test provides full force and energy curves during the millisecond of impact, using a "tup" that incorporates an impact head and a load cell. Common methods include ASTM D7192 and ISO 7765-2. Check out the information and video of testing in progress.
- Drop Impact: This test uses a single dart configuration and a single drop height, while varying the weight of the dart. It includes methods such as ASTM D1709 and ISO 7765-1. Here is some additional information on this test method.
- Slow Rate Penetration: During this test, a probe punctures the film at a slow cross-head speed of 10 in/min. Common methods for this test are ASTM F1306 and FTMS 101C/MIL-STD-3010C Method 2065.
To determine the test best for each application, it is important to understand the types of impact stress a film will experience. Three characteristics to consider when choosing a test procedure are location of impact, type of impact and speed of impact. Consider real examples:
- Medical Product Packaging: These products often shift inside the packaging, causing locational stresses. Impact occurs from the inside to the outside of the film at a slow rate.
- Roof Solar Panel Film: A solar panel is subject to falling debris with the location of impact happening from outside to inside by a falling drop. Speed is dictated by height of the drop.
- Storage Bag: One type of impact to consider is a storage bag shifting location within a closet or freezer. Impact can be from both internal and external sources and the speed of impact may be slower. Cold temperature testing may also be applicable.
When evaluating impact, choose the best test, or multiple tests, to match application forces for the product. Keep in mind: each of these standard procedures can be optimized through modifications of impact tup, speed and configuration. In the end, a clear understanding of potential hazards in the field and knowledge of available test procedures is the best way to design a test program to understand impact.